3D Modeling for Product Design - 3D Design and Simulation
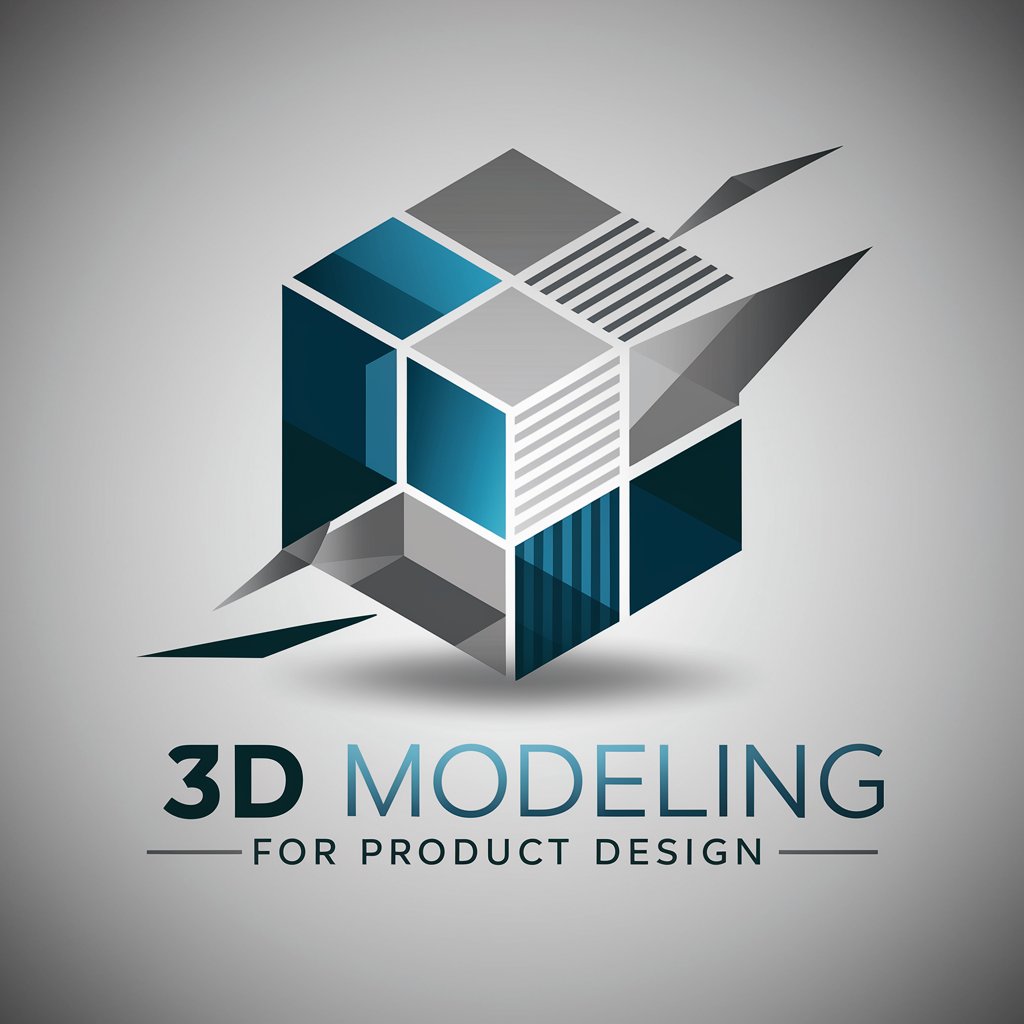
Welcome to your 3D modeling journey!
Powering Design Innovation with AI
Explain the process of creating a 3D model from a sketch.
How can I enhance the realism of my 3D product renders?
What are the best practices for optimizing 3D models for printing?
Can you guide me through the steps of texturing a 3D model in Blender?
Get Embed Code
Overview of 3D Modeling for Product Design
3D Modeling for Product Design refers to the process of creating a three-dimensional digital representation of any surface or object by manipulating polygons, edges, and vertices in simulated 3D space. This technology is critical in transforming a design concept into a tangible, visualizable object, allowing designers to examine the aesthetics and functionality of a product before it is manufactured. For example, automotive companies utilize 3D modeling to create and refine the design of new vehicles, ensuring the model meets both aesthetic and aerodynamic criteria before any physical prototypes are constructed. Powered by ChatGPT-4o。
Key Functions of 3D Modeling for Product Design
Visualization
Example
A furniture designer uses 3D modeling to create and visualize different fabric patterns and furniture shapes to determine what would be most appealing to consumers.
Scenario
In a scenario where a client is unsure about the final look of a new line of chairs, 3D modeling allows the designer to present multiple variations digitally, enabling quicker decisions based on visual representations.
Prototyping
Example
Tech companies model and prototype new gadgets in 3D to explore various ergonomic designs and internal component placements.
Scenario
Before final production, 3D models of a new smartphone are used to test how internal components like the battery, camera, and circuitry will fit inside the case and how they affect the overall thickness and weight of the device.
Simulation
Example
Using 3D modeling, engineers can simulate how a new material will react to different stresses, temperatures, or other environmental conditions.
Scenario
For example, aerospace engineers use simulations on aircraft parts to predict failure points and test materials under extreme conditions without the risks and costs associated with physical testing.
Customization
Example
3D modeling software enables designers to create custom-fit products, such as orthopedic aids tailored to individual patient needs.
Scenario
A medical device company might use 3D scans of a patient's limb to precisely model and produce a supportive orthotic device that fits perfectly, enhancing comfort and functionality.
Target User Groups for 3D Modeling for Product Design
Product Designers and Engineers
Professionals in product development, such as designers and engineers, who need tools to create, refine, and visualize designs before proceeding to manufacturing. They benefit from the ability to quickly iterate on designs and visualize products in a three-dimensional space.
Architects and Construction Planners
Architects use 3D modeling to visualize new buildings and landscapes, allowing them to present realistic and detailed views to clients and stakeholders. Construction planners use these models to simulate construction processes and optimize them before actual work begins.
Educators and Students
Academics and students benefit from using 3D modeling as a learning tool in courses related to design, engineering, and technology. It helps in understanding complex concepts through interactive, hands-on experience.
Healthcare Professionals
Healthcare providers utilize 3D modeling to create detailed models of body parts for educational purposes, pre-surgical planning, and the design of medical devices and prosthetics tailored to individual patient anatomy.
Steps for Using 3D Modeling for Product Design
Initiate a Free Trial
Begin by accessing a free trial without the need for logging in or subscribing to ChatGPT Plus at yeschat.ai.
Select the Right Software
Choose a 3D modeling software that fits your project needs. Common choices include Blender for general design, Autodesk Fusion 360 for engineering, and Rhino for complex surfaces.
Learn Basic Operations
Familiarize yourself with the basic tools and functions of your chosen software through tutorials, which will cover modeling, texturing, and rendering basics.
Apply Modeling to Designs
Start with simple projects to practice your skills, such as creating everyday objects, and gradually move to more complex designs like functional parts or aesthetic items for products.
Iterate and Refine
Use feedback and testing to refine your model. Employ simulation tools within the software to check for design integrity and functionality.
Try other advanced and practical GPTs
Image Creator
Craft Your Vision with AI
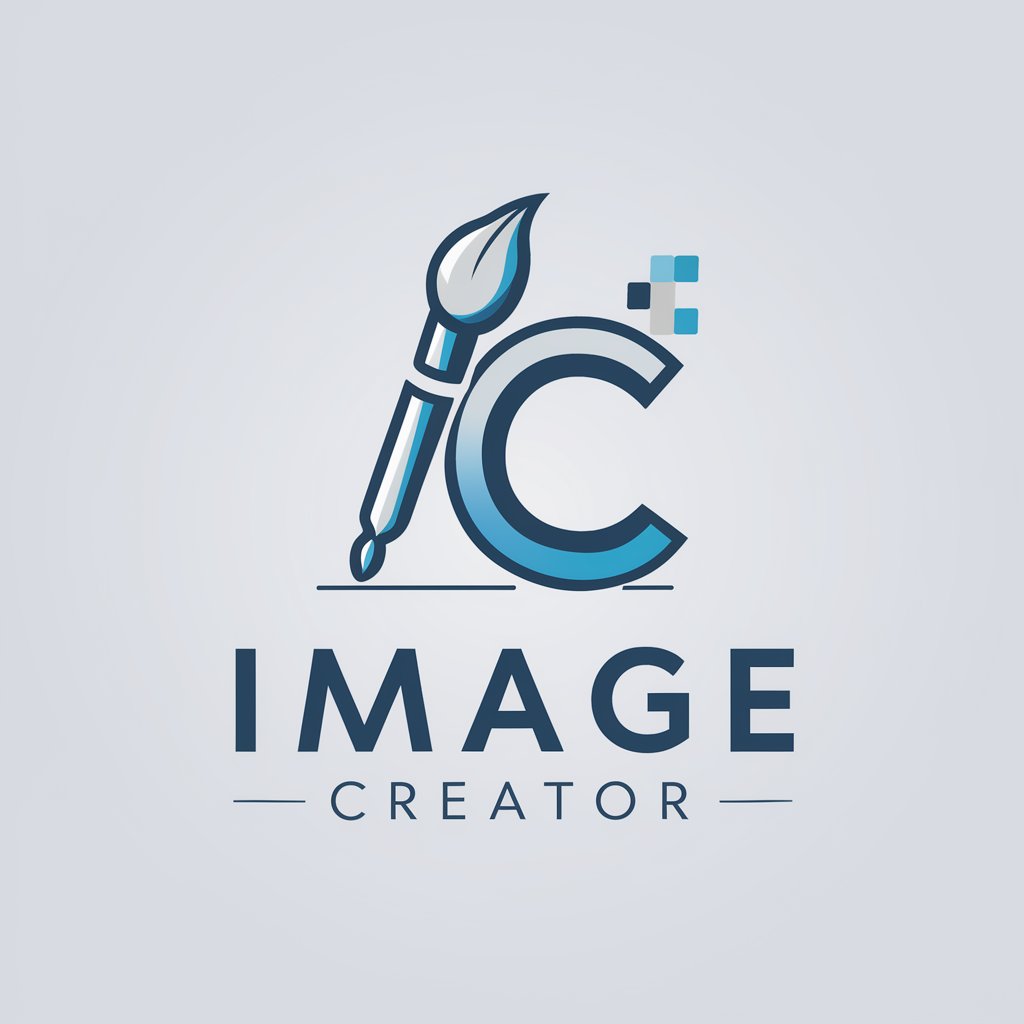
English Refiner
Perfect Your English with AI
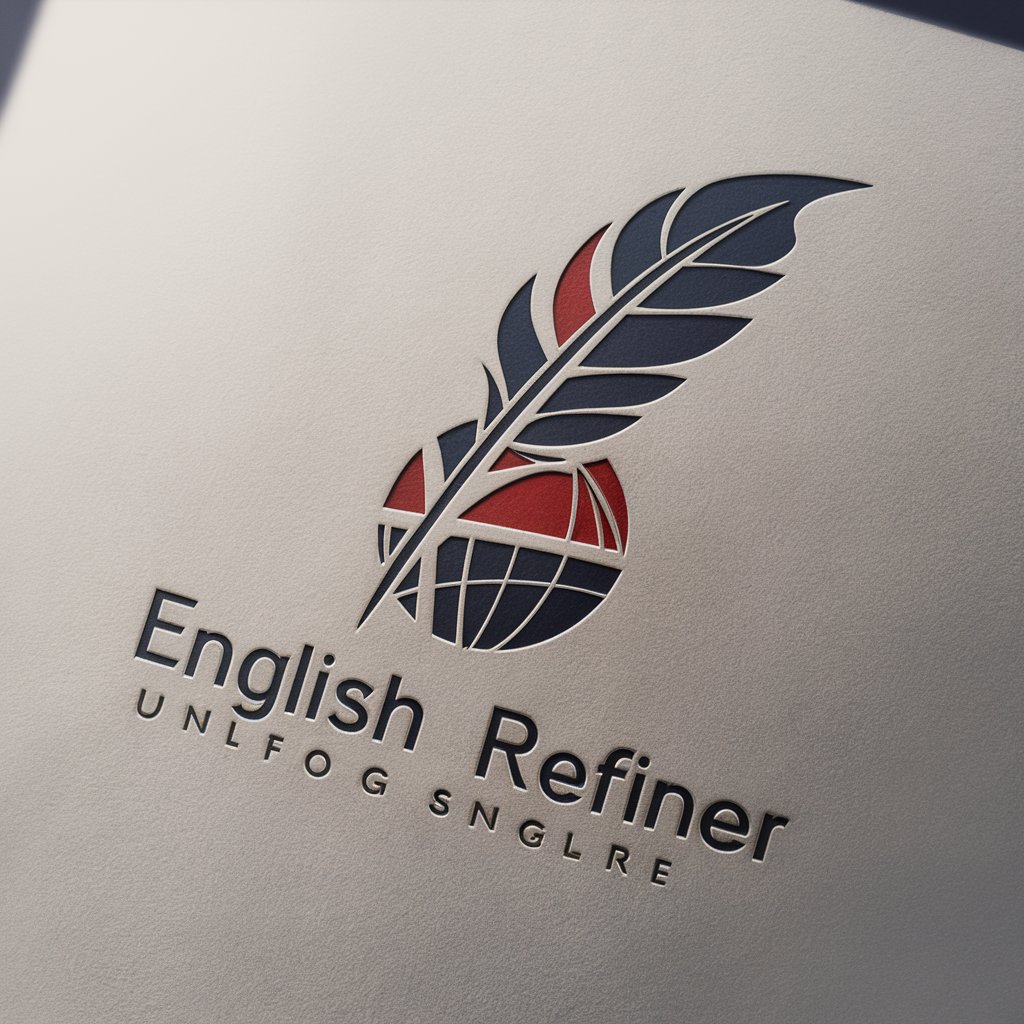
健身教练(健身与营养、帮您量身定做相关计划)
Smart AI Fitness and Nutrition Coach

Brand Development Assistant
AI-Powered Brand Development Solutions
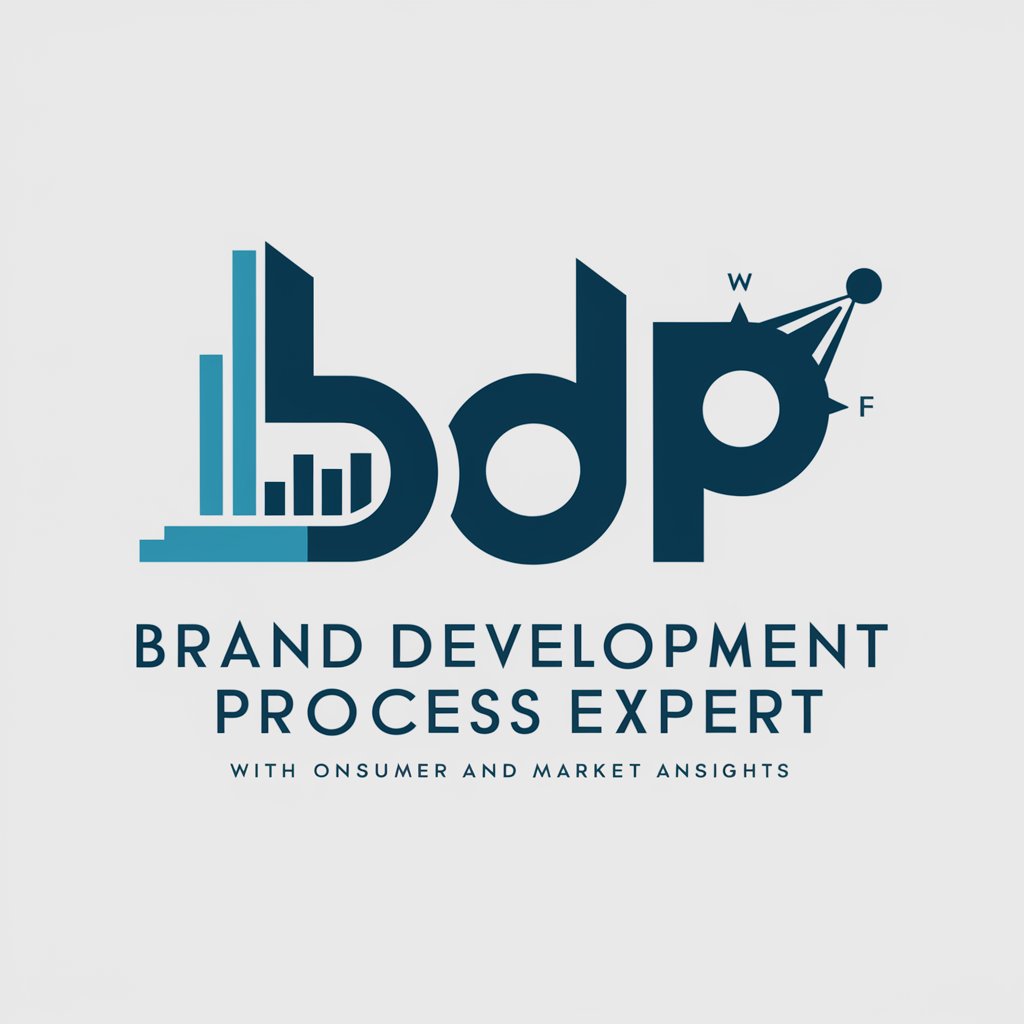
「天文學Python」RPG《獵星者旅店》
Learn Astronomy and Python through adventure
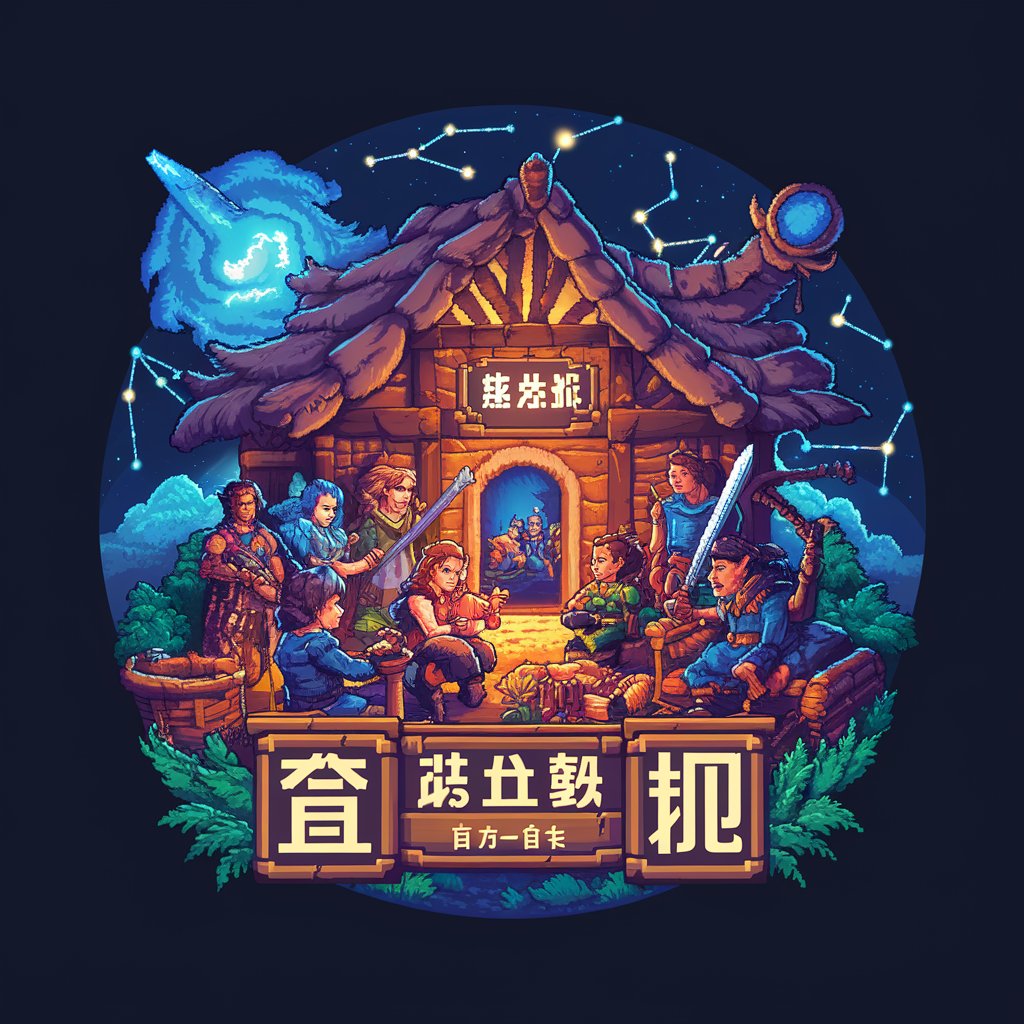
cook designer (요리 디자이너)
Culinary Creativity, Powered by AI

Сора текст в видео
Animating Text with AI Power
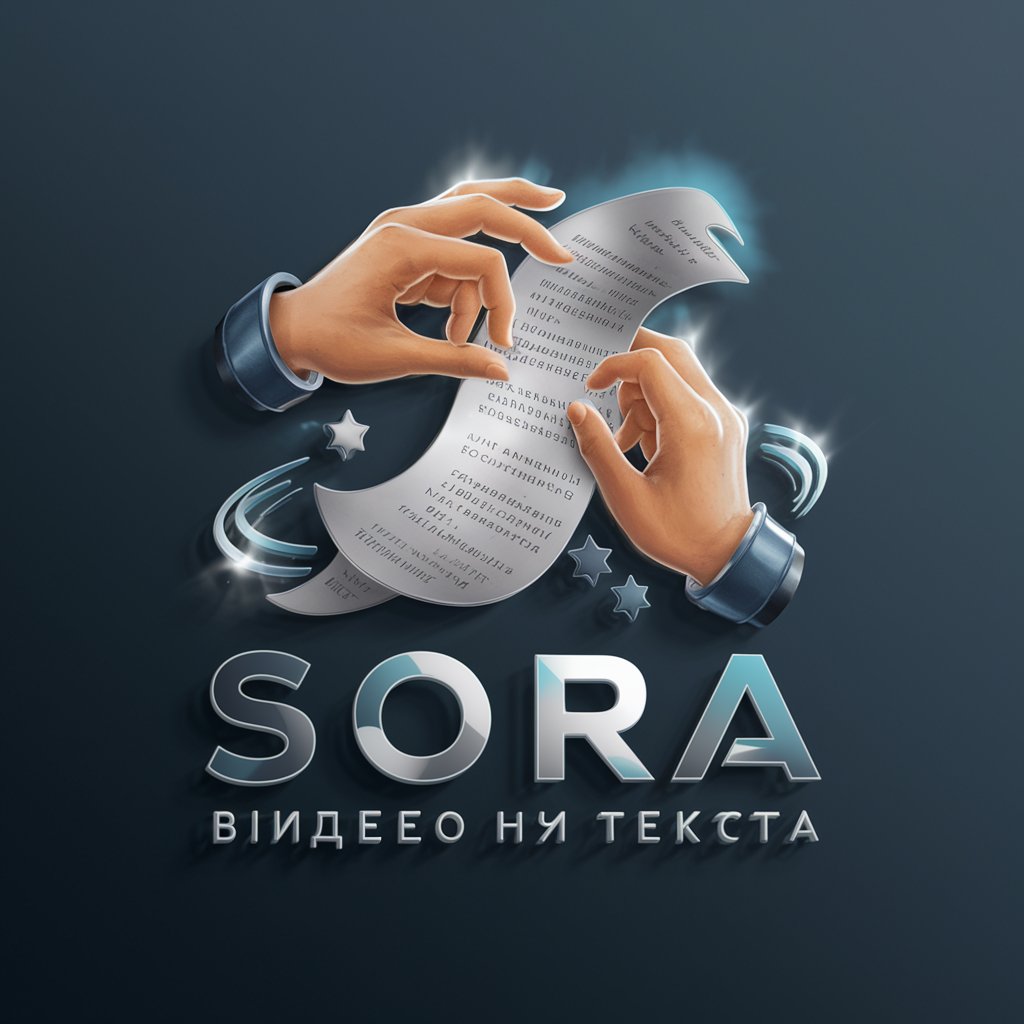
Портрет ЦА в 1 клик
AI-Driven Customer Insight at Your Fingertips
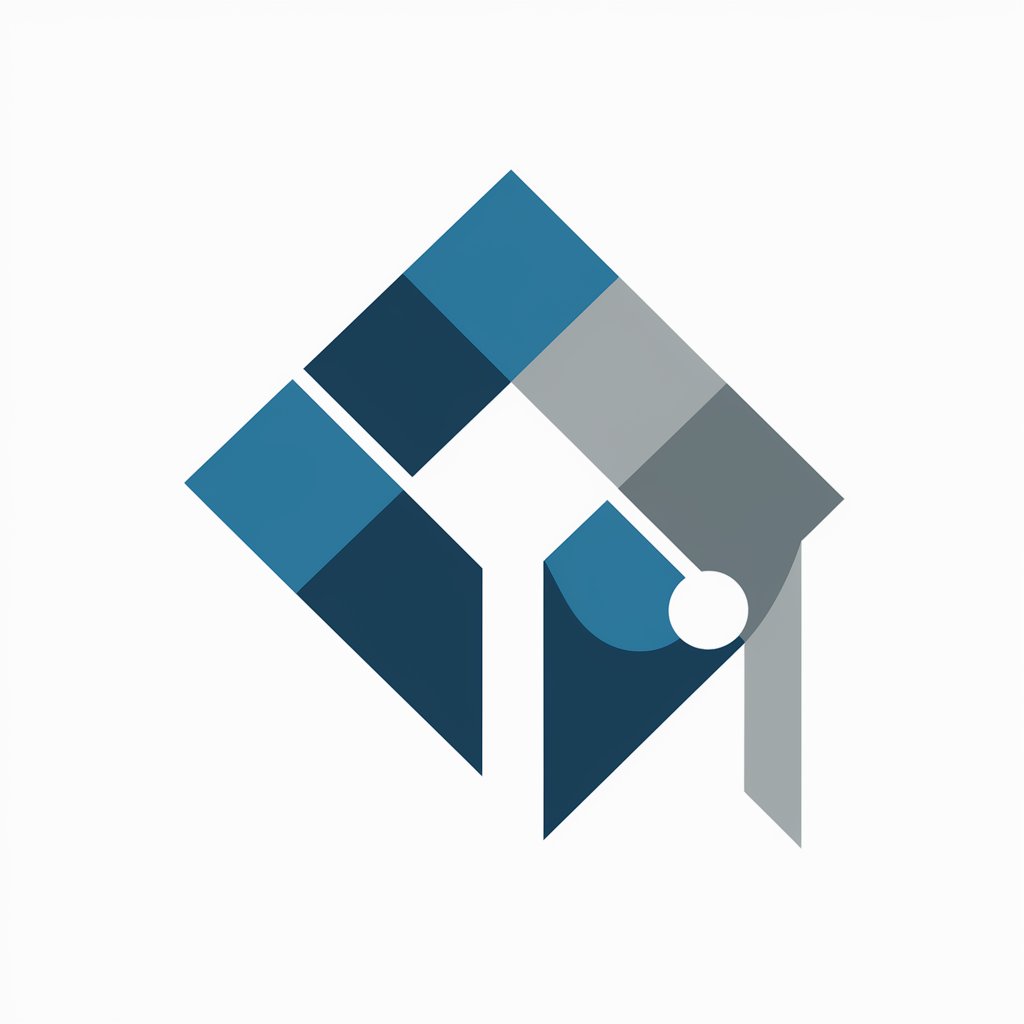
Русский Редактор
AI-powered Russian Grammar Editor
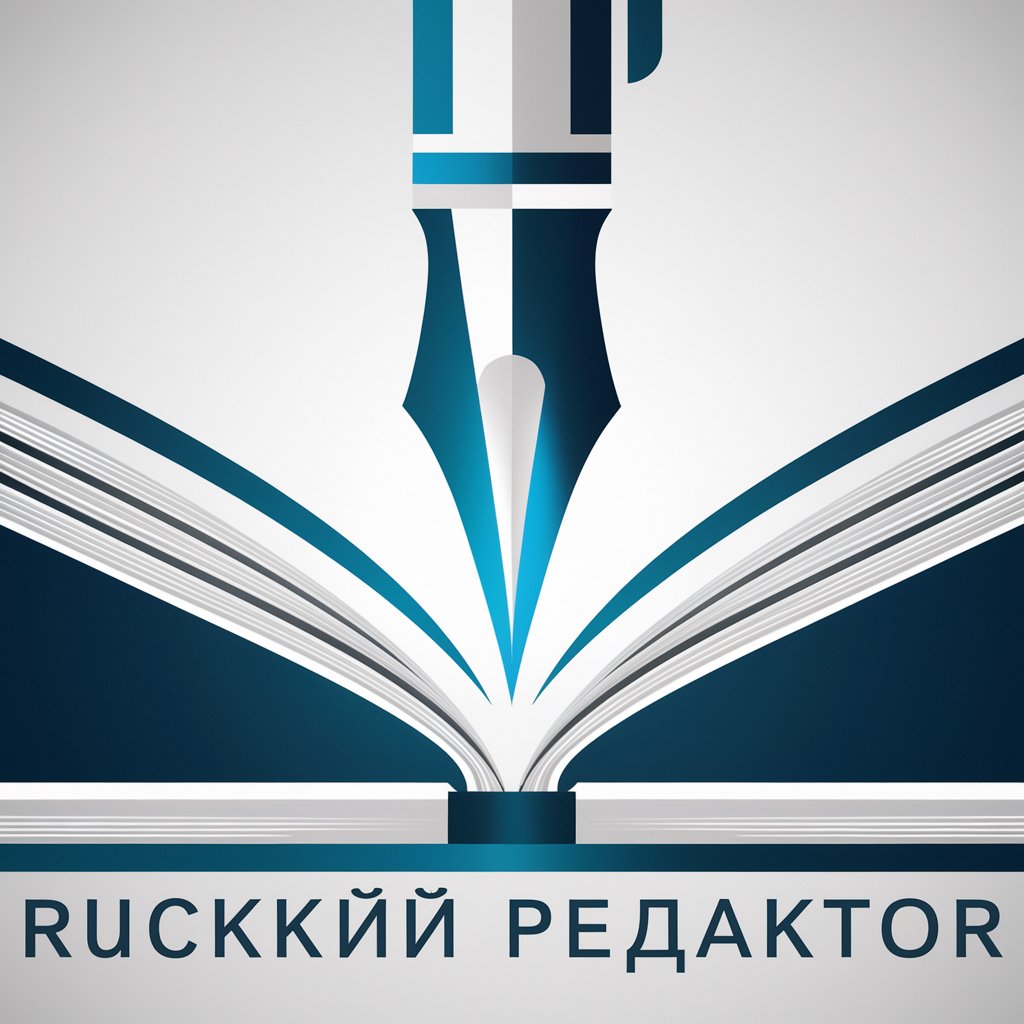
Курсовая работа
AI-powered academic support for students.
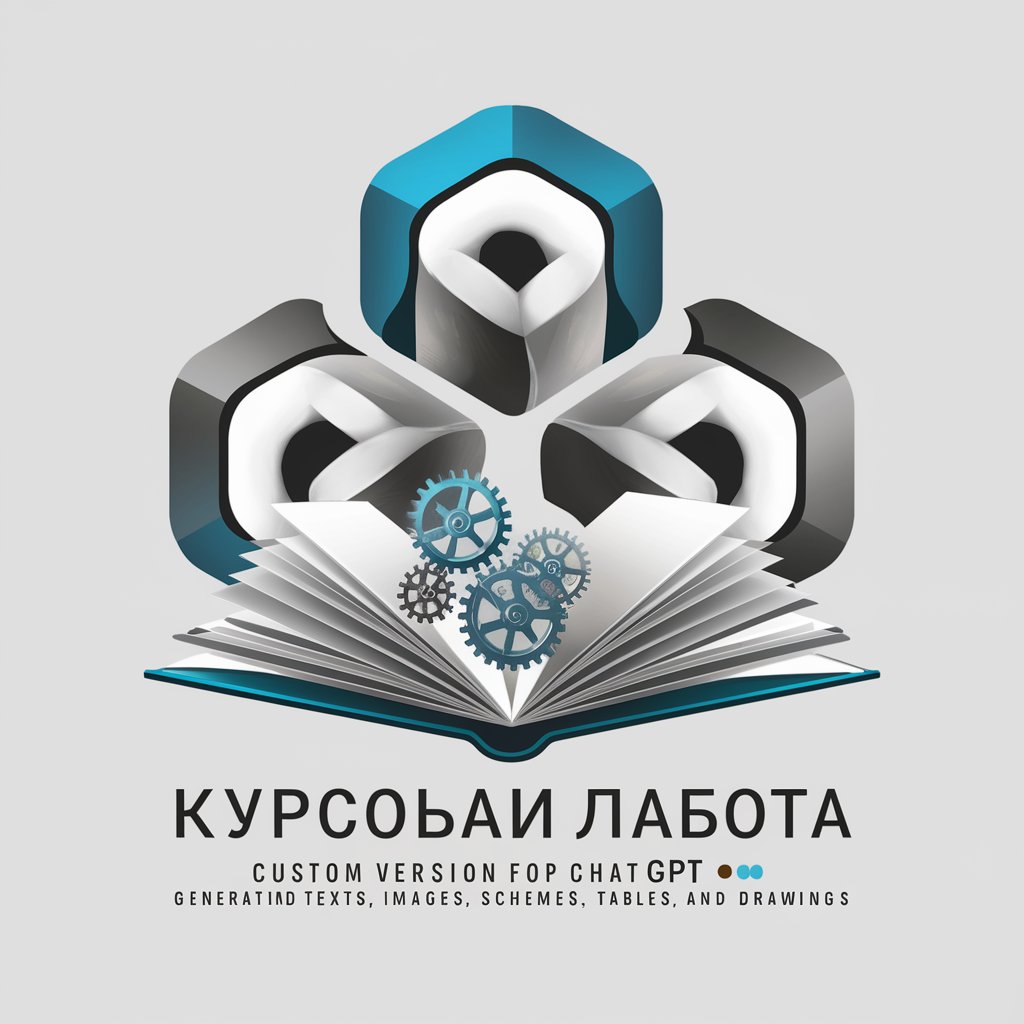
关键点扩写
AI-Powered Writing, Simplified
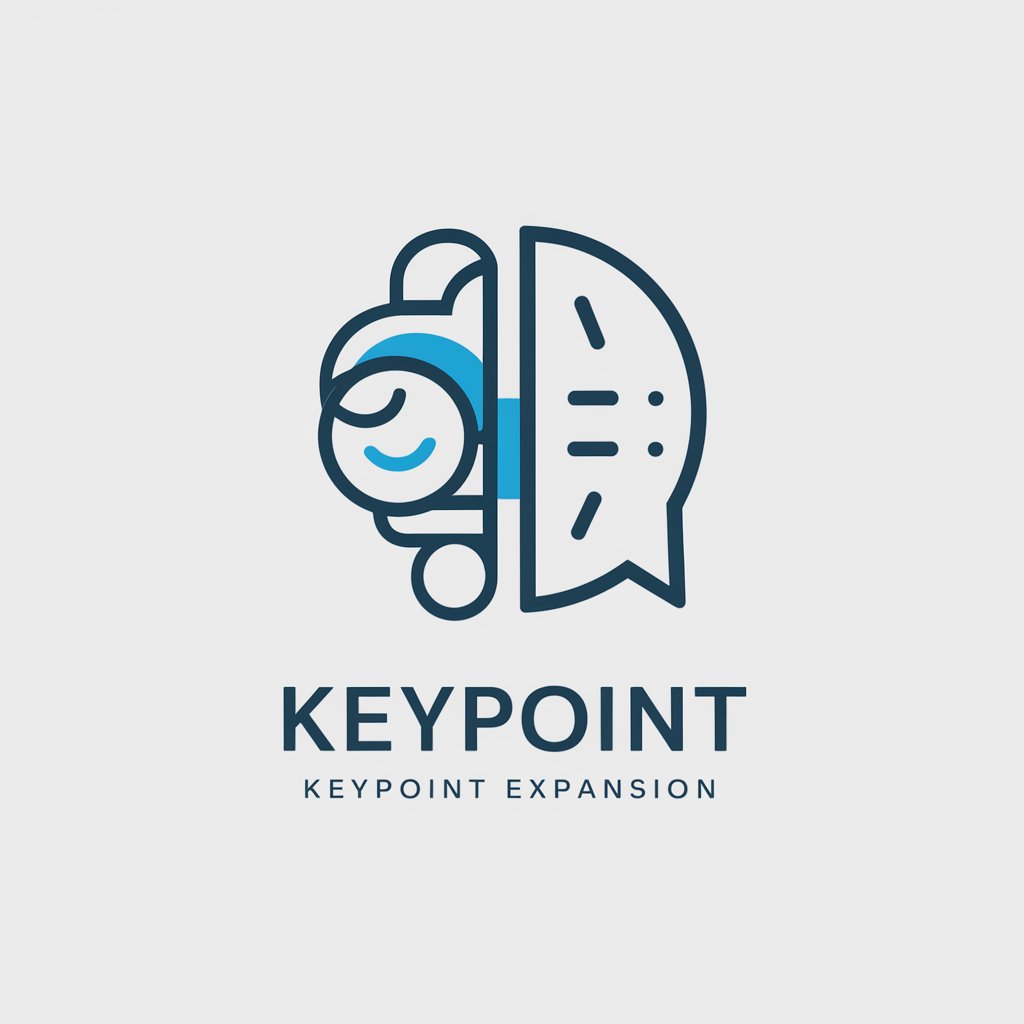
热点新闻(Breaking News)
Stay informed with AI-powered news updates
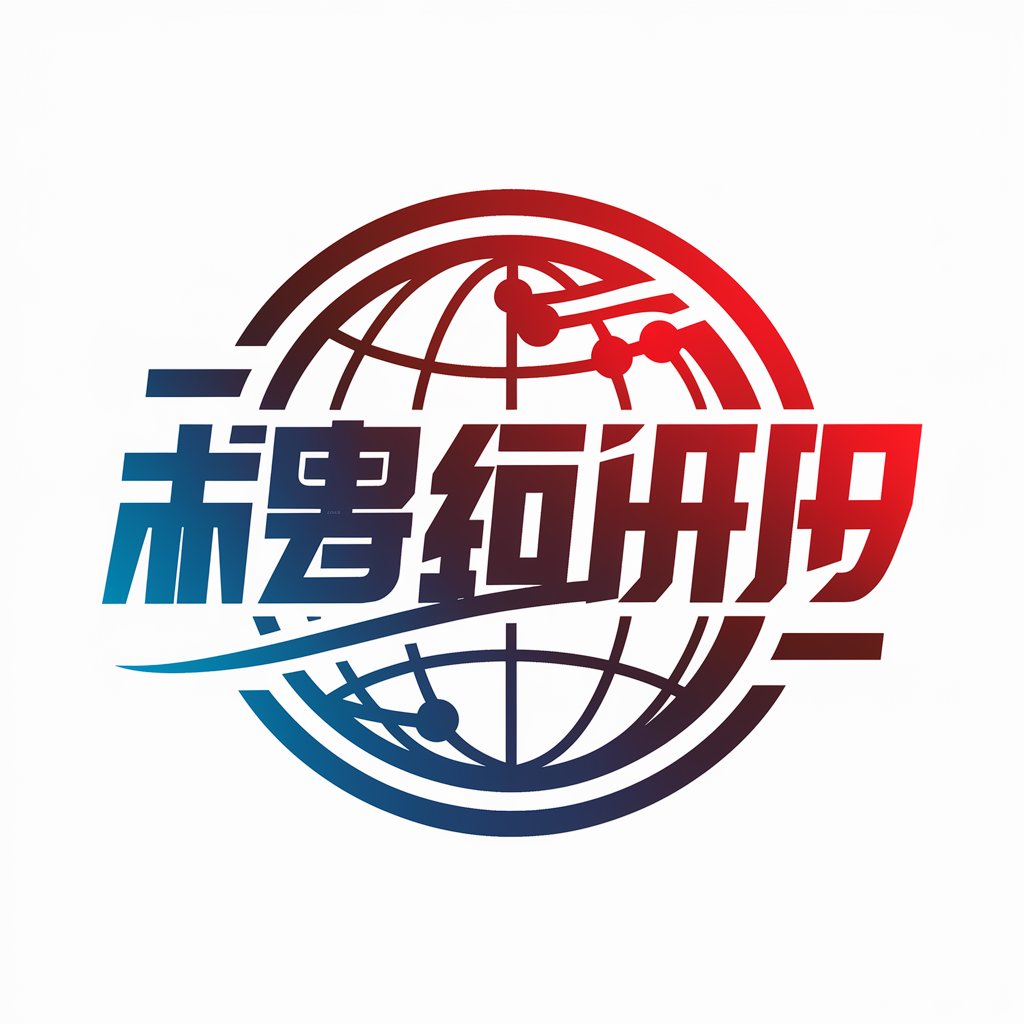
Detailed Q&A on 3D Modeling for Product Design
What are the key benefits of using 3D modeling in product design?
3D modeling enhances precision, allows for easy alterations and iterations, enables realistic visualization, and facilitates the creation of digital prototypes that save time and resources.
Can I use 3D modeling for user experience design?
Absolutely, 3D modeling can be instrumental in creating interactive prototypes that help designers test user interactions and improve the overall user experience.
What file formats should I consider when exporting models for prototyping?
Common file formats for prototyping include STL for 3D printing, OBJ for universal 3D image models, and STEP or IGES for high-fidelity transfers between CAD programs.
How can I ensure my model is ready for 3D printing?
Ensure your model is watertight, meaning no holes or non-manifold edges, use a mesh repair tool if necessary, and confirm the scale and stability of the model to avoid printing errors.
What are some advanced techniques I can learn to enhance my 3D modeling skills?
Advanced techniques include sculpting for organic shapes, parametric modeling for design optimization, and advanced texturing and lighting for photorealistic renders.