fibre reinforced composites - Easy Composite Design
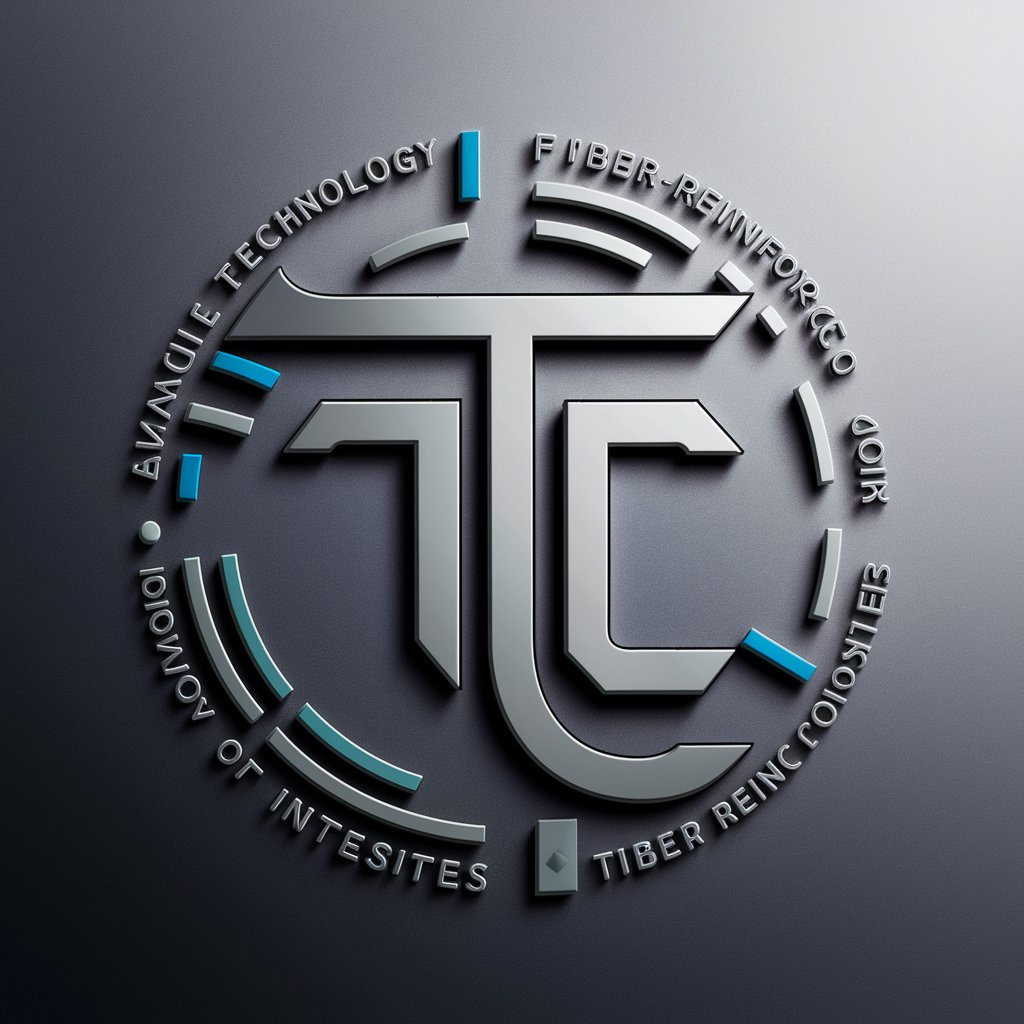
Welcome to your textile technology resource.
AI-Powered Composite Innovation
Analyze the impact of fiber length on the mechanical properties of composites.
Summarize recent advancements in natural fiber-reinforced composites.
Discuss the role of fiber content in the performance of polymer composites.
Review the findings on the environmental benefits of natural fiber composites.
Get Embed Code
Introduction to Fibre Reinforced Composites
Fibre reinforced composites (FRCs) are advanced materials formed by combining fibres with a matrix material to enhance strength and elastic properties. The fibres, typically made from carbon, glass, aramid, or natural substances, provide structural strength and stiffness. The matrix, often a polymer, metal, or ceramic, binds the fibres together, transferring stress between fibres and protecting them from environmental damage. FRCs are designed to exploit the high strength and modulus of fibres while compensating for their weaknesses through the matrix material. This combination results in materials with superior properties than the individual components alone. For example, carbon fibre reinforced polymer (CFRP) composites are renowned for their high strength-to-weight ratio, making them ideal for aerospace structures where weight reduction is critical without compromising strength. Powered by ChatGPT-4o。
Main Functions of Fibre Reinforced Composites
Enhanced Strength and Stiffness
Example
Carbon Fibre Reinforced Polymer (CFRP) used in aerospace components
Scenario
In aerospace engineering, CFRP composites are used to manufacture critical load-bearing structures, such as wings and fuselage sections, offering significant weight savings and fuel efficiency improvements over traditional materials like aluminum.
Corrosion Resistance
Example
Glass Fibre Reinforced Polymer (GFRP) rebars in concrete structures
Scenario
GFRP rebars are employed in bridge decks and marine structures exposed to harsh environments. Unlike steel, GFRP does not corrode, extending the lifespan of concrete structures while reducing maintenance costs.
High Fatigue Resistance
Example
Aramid Fibre Reinforced Composites in bulletproof vests
Scenario
For personal protection equipment such as bulletproof vests, aramid fibre composites provide not only high strength and puncture resistance but also the ability to absorb and disperse energy, ensuring durability and longevity under repeated stress or impact.
Thermal Insulation
Example
Carbon and Glass Fibre Reinforced Composites in spacecraft
Scenario
Spacecraft utilize FRCs for their thermal insulation properties, protecting sensitive instruments and crew from the extreme temperatures encountered in space missions, ranging from the intense heat of re-entry to the cold vacuum of space.
Ideal Users of Fibre Reinforced Composites Services
Aerospace Engineers and Manufacturers
These professionals rely on FRCs for constructing lightweight, high-strength aircraft components. The significant weight savings translate to enhanced fuel efficiency and payload capacity, pivotal in the competitive aerospace sector.
Civil Engineers and Construction Industry Professionals
This group benefits from the durability and corrosion resistance of FRCs, using them in bridges, buildings, and infrastructure projects to achieve longer lifespans and reduced maintenance requirements.
Defense and Security Sector
Military and law enforcement agencies use FRCs for personal protective equipment, vehicle armor, and lightweight, durable components for military hardware, valuing the material's strength, impact resistance, and fatigue properties.
Sports and Recreational Equipment Manufacturers
Manufacturers of high-performance sporting goods such as bicycles, tennis rackets, and golf clubs utilize FRCs to produce lightweight, high-strength equipment that enhances athlete performance and equipment durability.
How to Use Fibre Reinforced Composites
1
Start by exploring options at yeschat.ai for a hassle-free experience, accessible without any login or subscription to ChatGPT Plus.
2
Select the appropriate fibre type and composite material based on your specific project requirements, considering factors such as tensile strength, flexibility, and environmental resistance.
3
Design the composite structure, taking into account the loading conditions and the desired shape, ensuring the fibre orientation maximizes the mechanical properties of the composite.
4
Fabricate the composite using suitable methods such as hand lay-up, resin transfer molding, or compression molding, ensuring a uniform distribution of fibres and minimal voids.
5
Test the final product under simulated service conditions to validate its performance, making adjustments to the design or fabrication process as necessary for optimal results.
Try other advanced and practical GPTs
Formula First Reinforce Mentor
Empowering AI-driven reinforcement learning exploration.

Reinforce Mentor
Empowering RL Projects with AI-Powered Insights
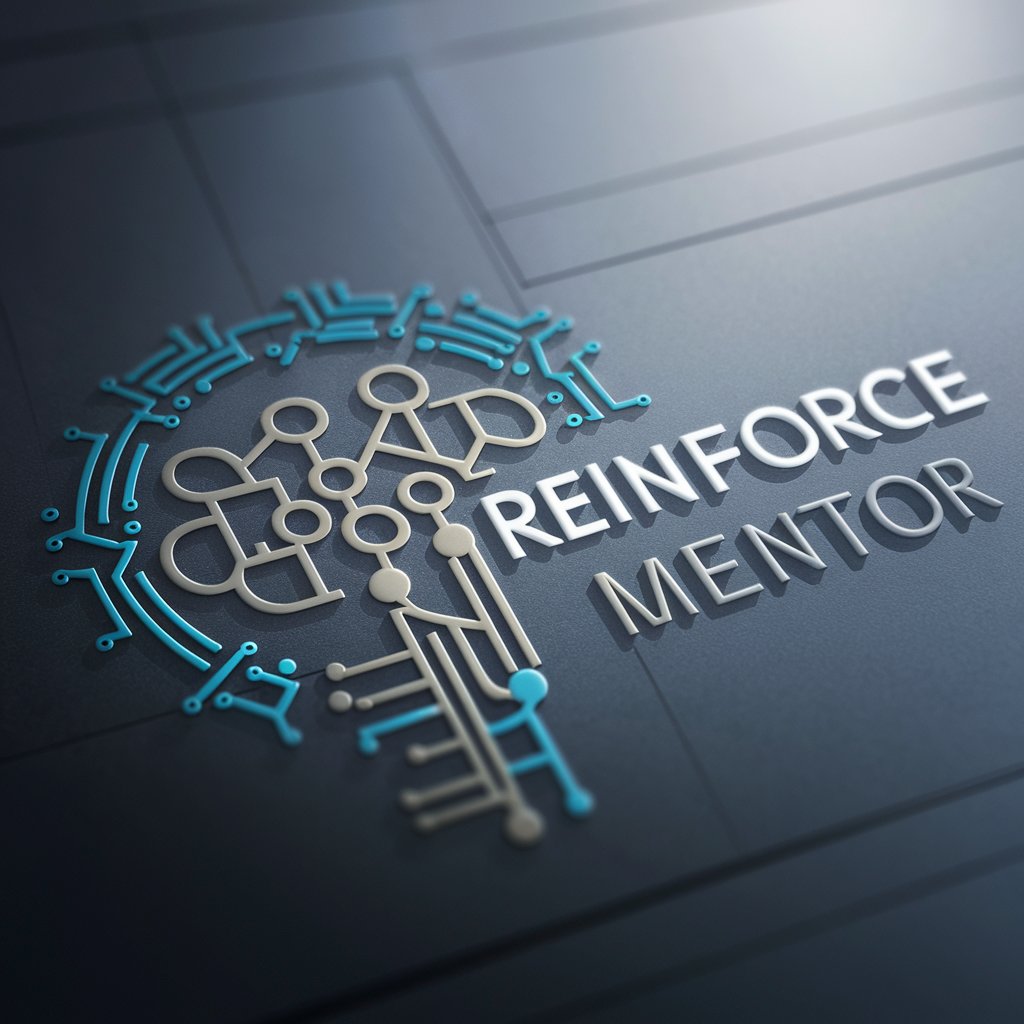
Reinforce Master
Master reinforcement learning with AI-powered guidance.
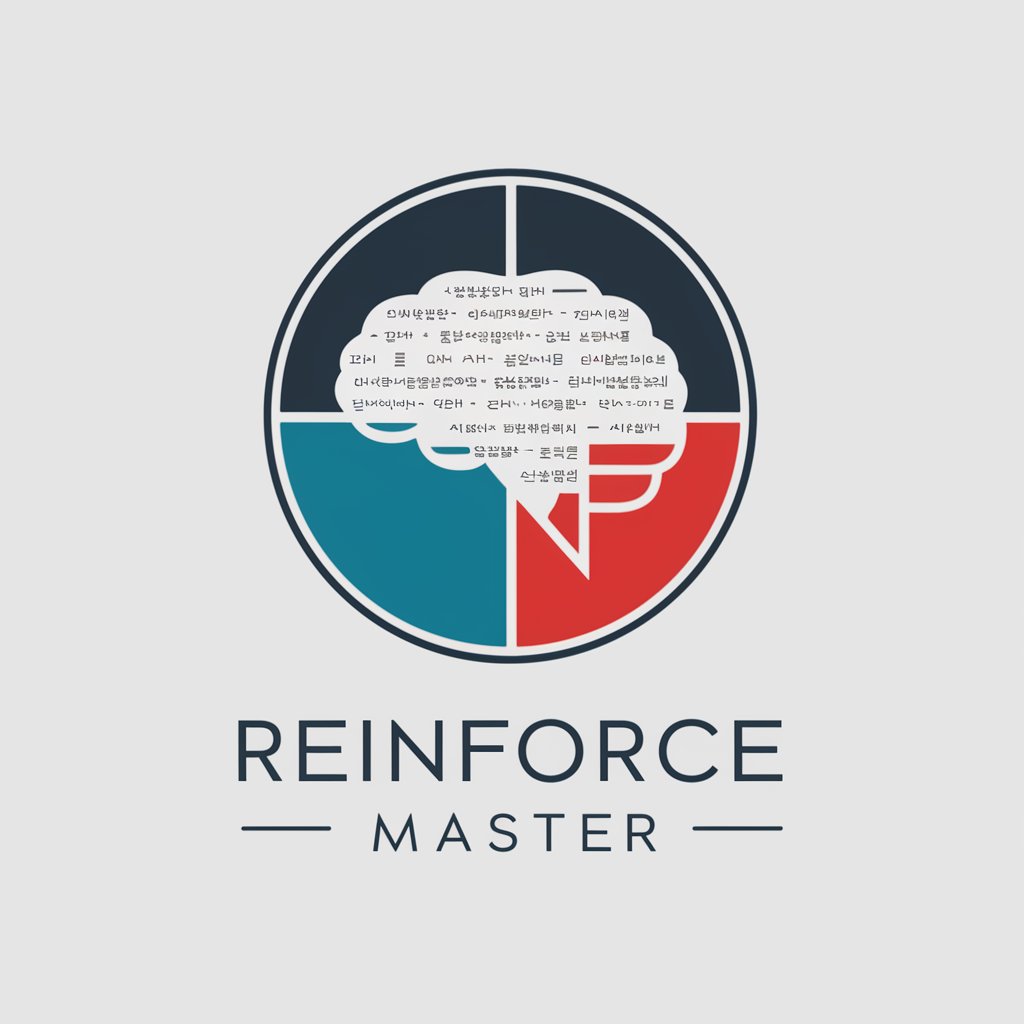
Advanced Reinforced Concrete Structures Tutor
Empowering concrete understanding with AI
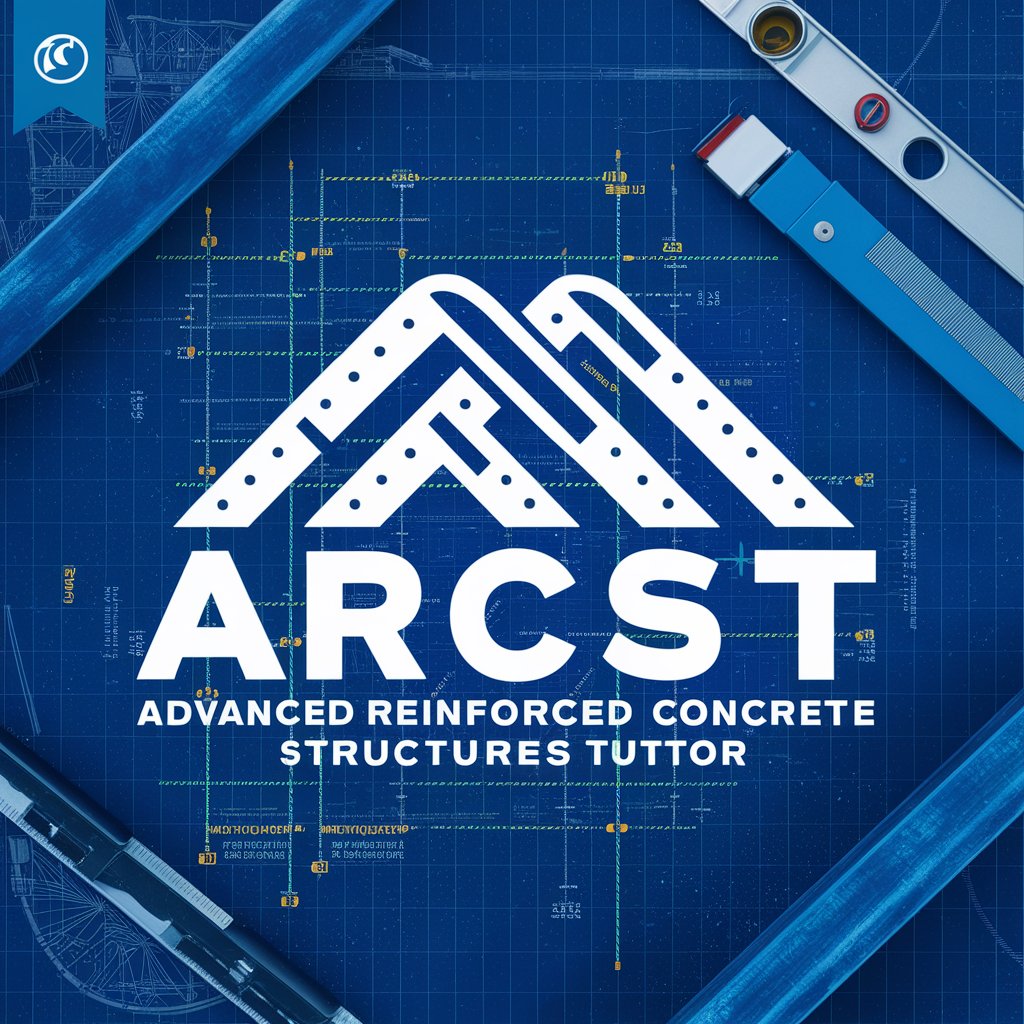
Reinforced Masonry Design Tutor
Design Smarter with AI-Powered Masonry Guidance
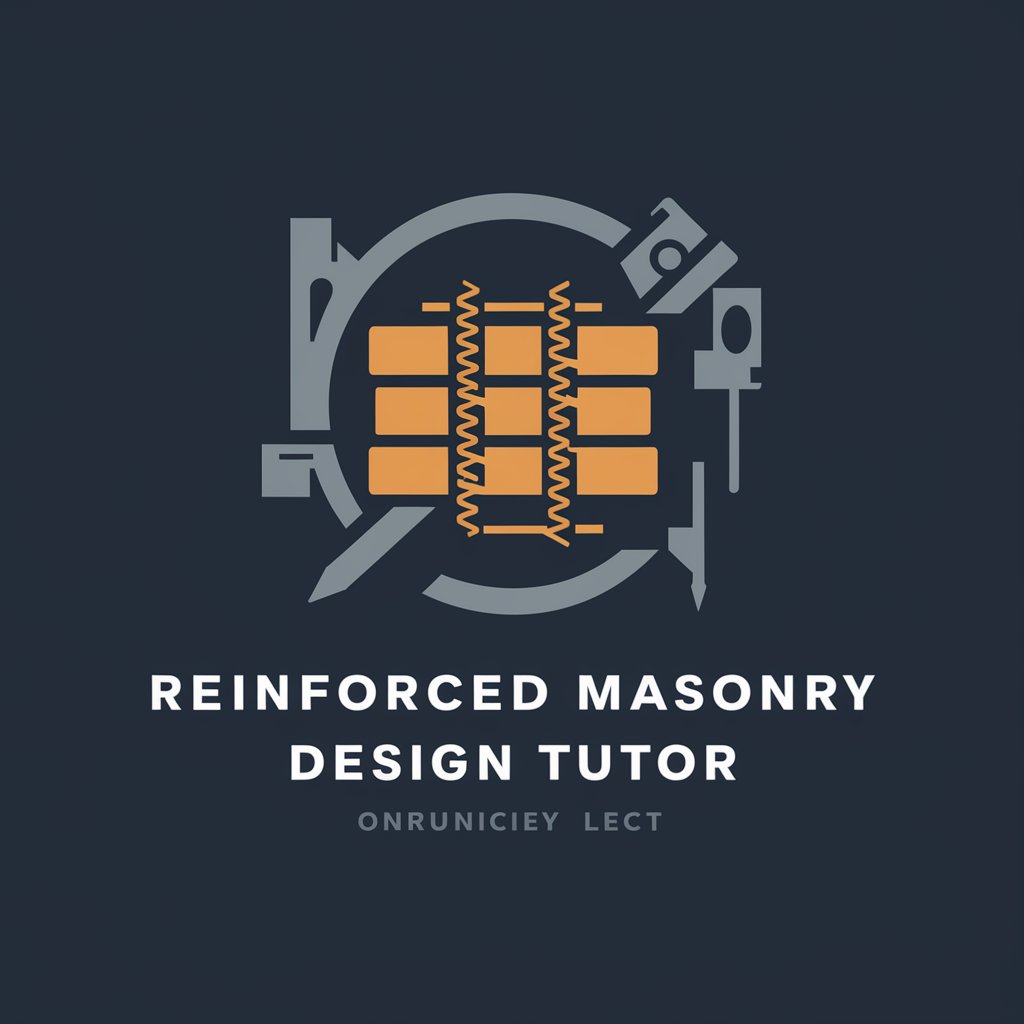
Viral Linkedin Post Formatter
AI-Powered LinkedIn Post Refinement
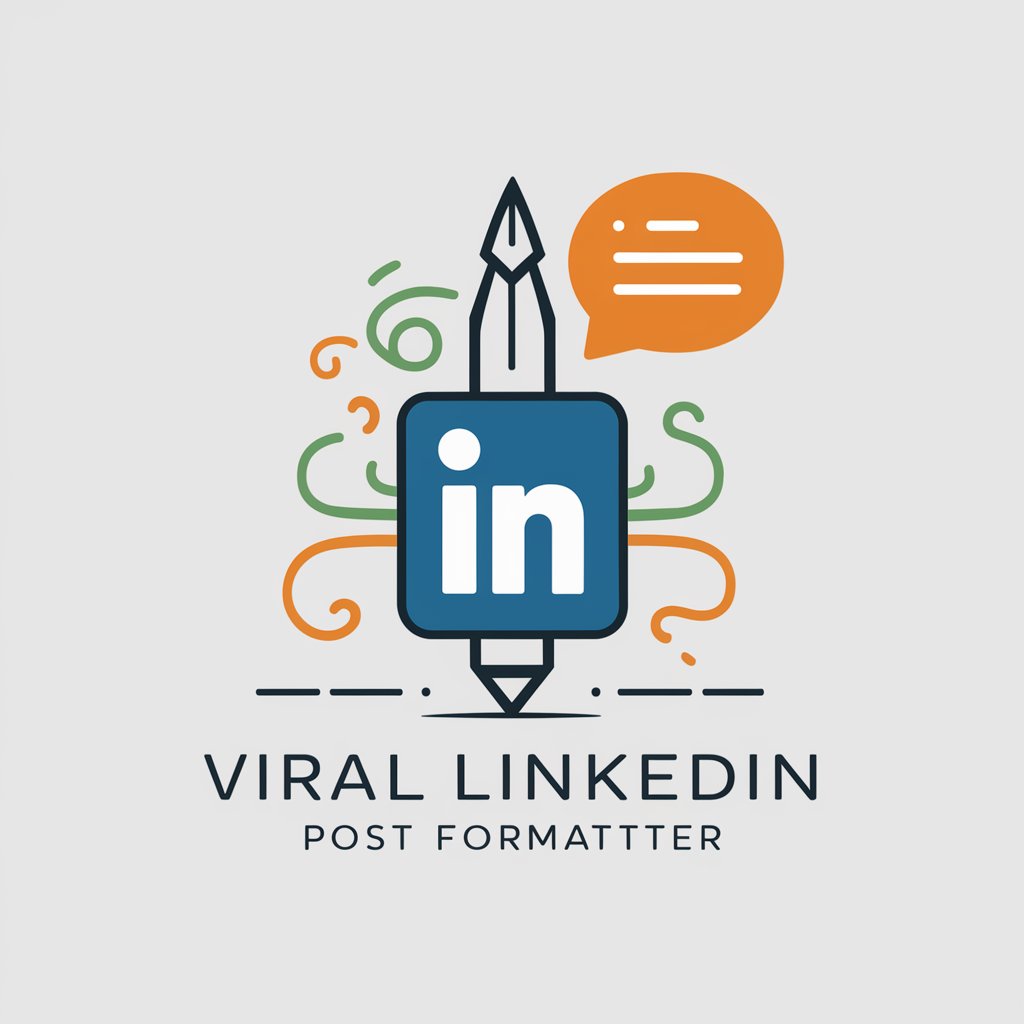
Reinforcement Learning Assistant
Empowering Reinforcement Learning with AI
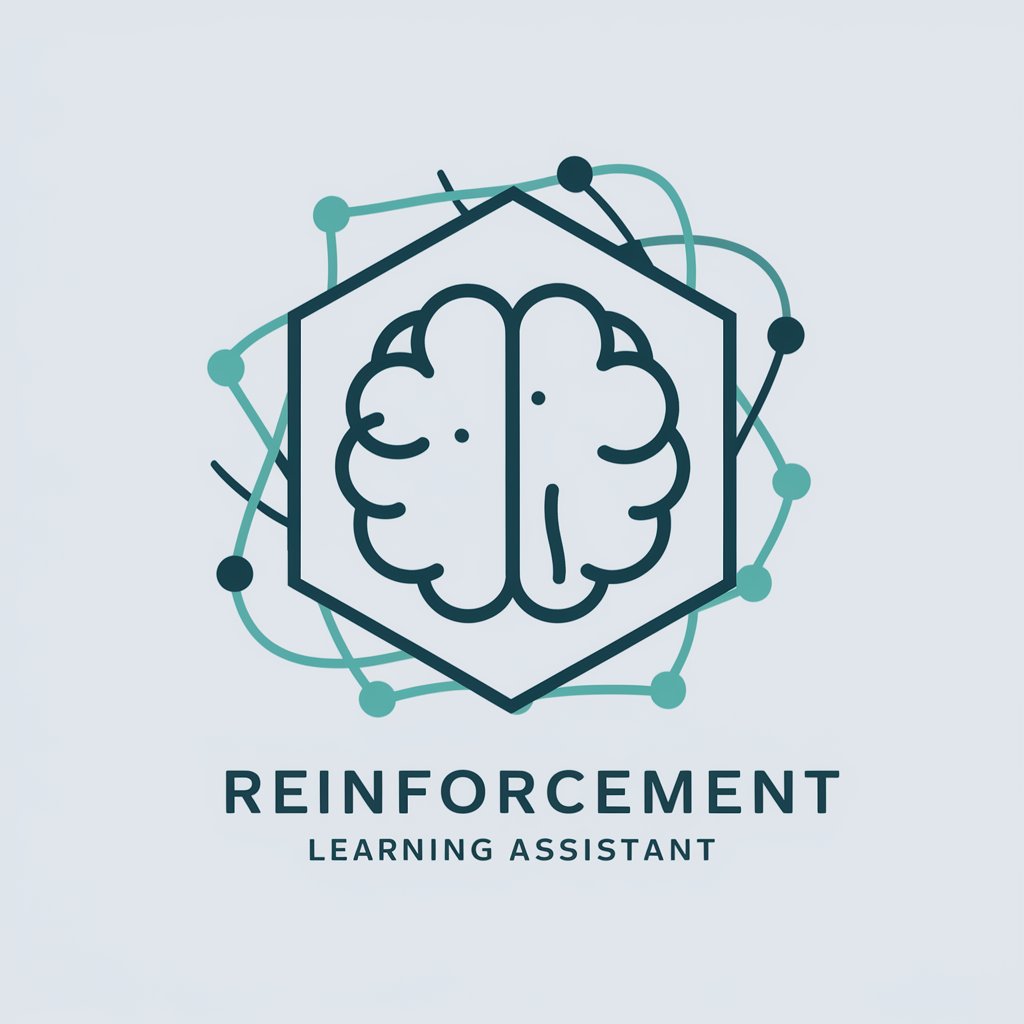
📚 Ada Package Master
Powering Ada development with AI
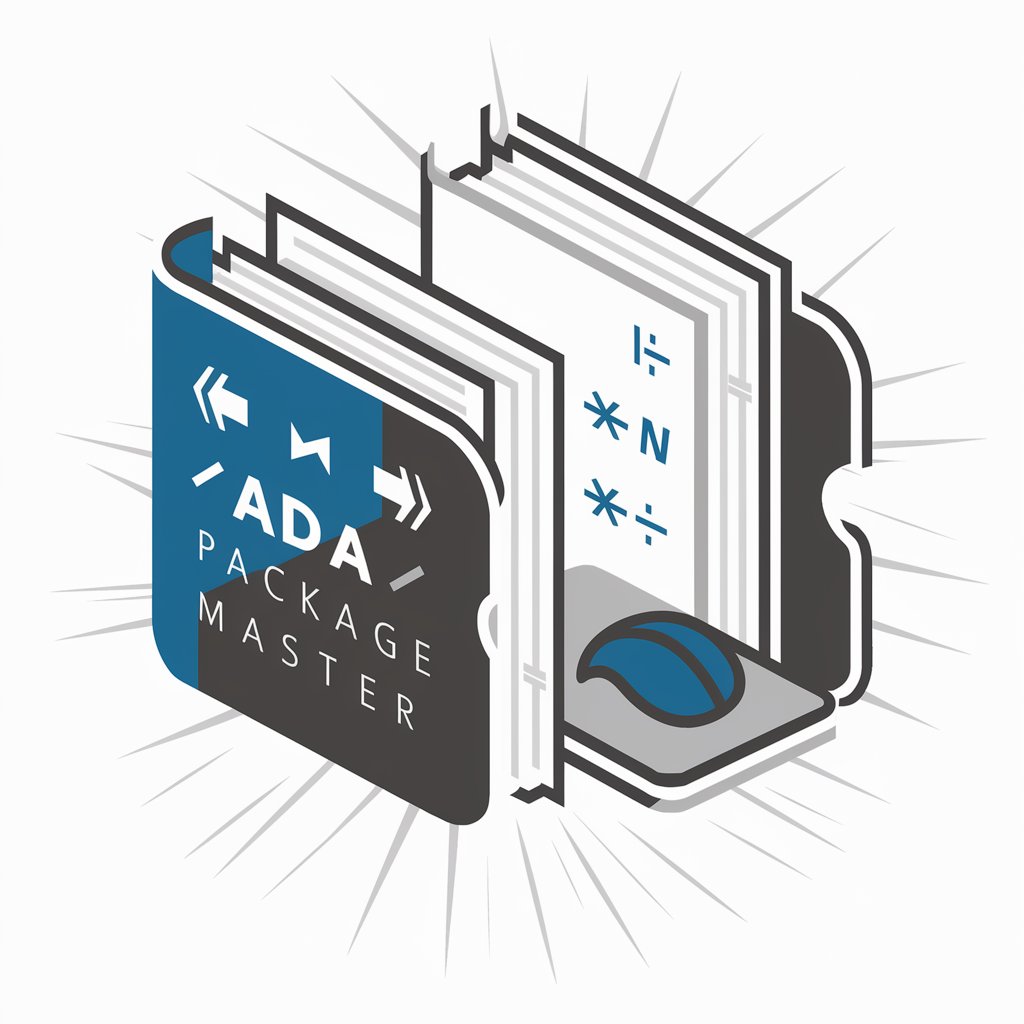
Lab Package Assistant
Optimize Lab Workflows with AI
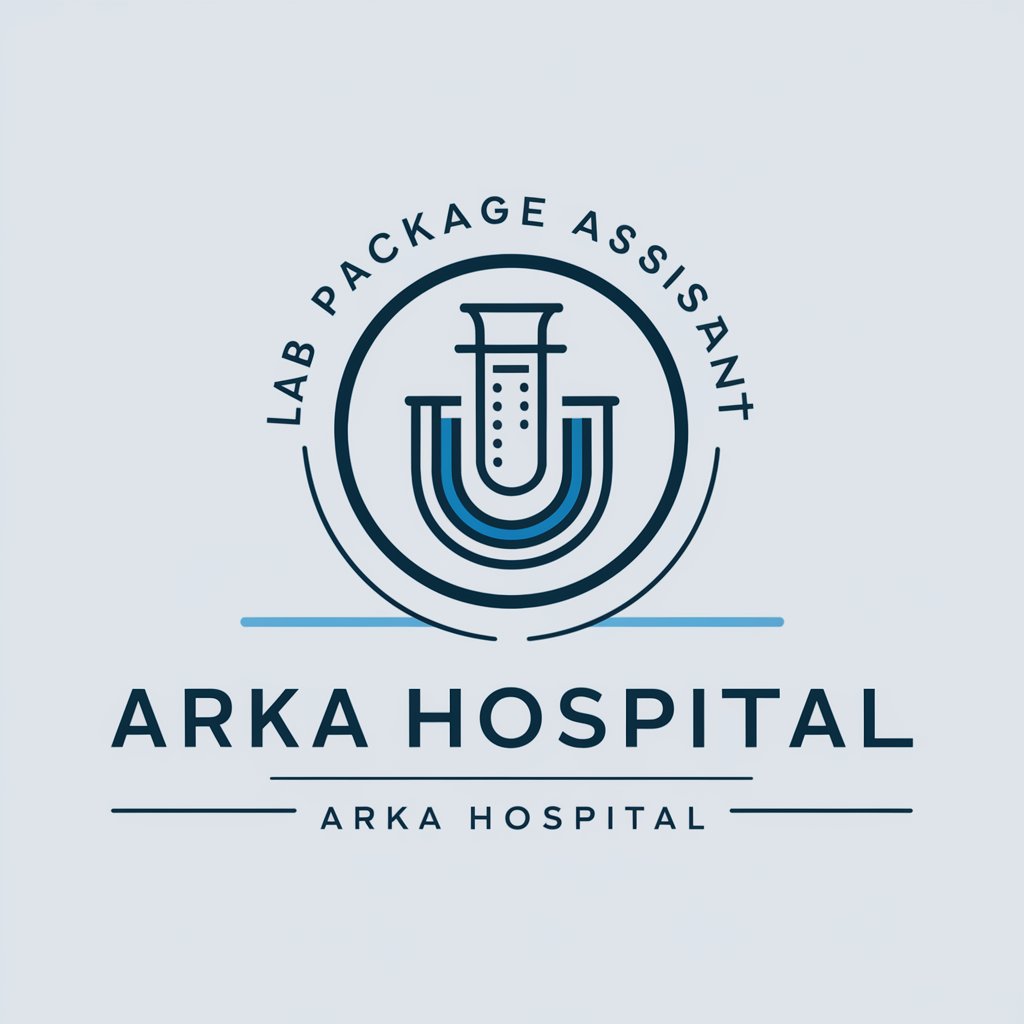
Starter package Expert
Empowering Businesses with AI-Driven Marketing Solutions

Package Evaluator
AI-driven code optimization at your fingertips.
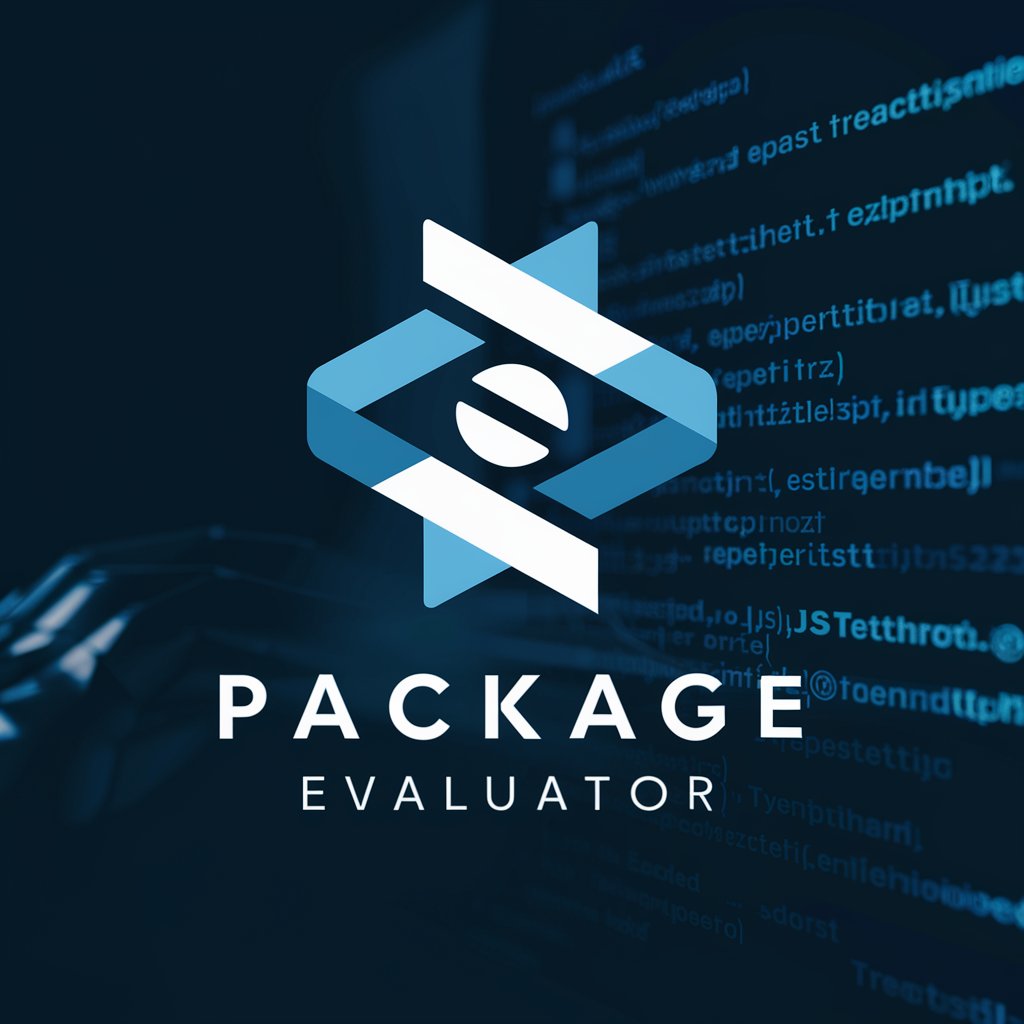
Django Package Advisor
AI-powered Django Package Guidance
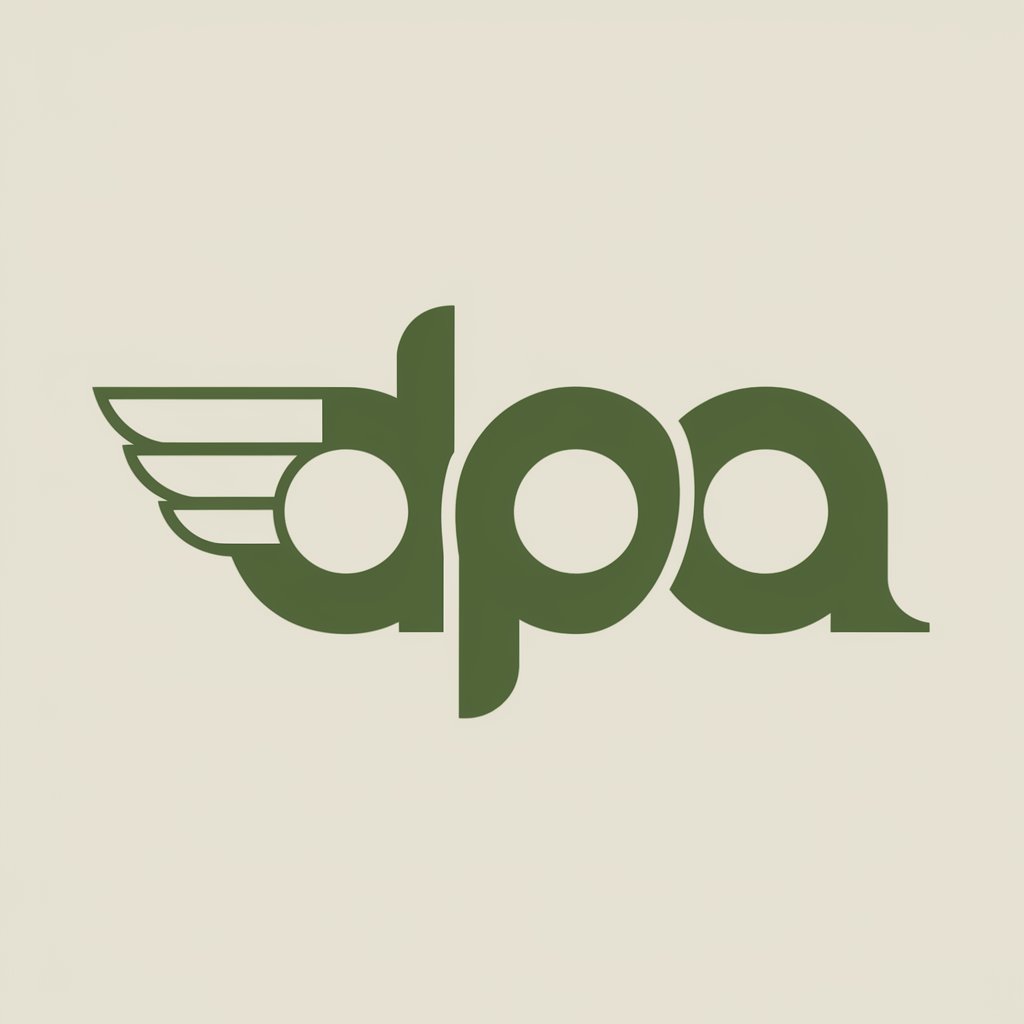
Frequently Asked Questions about Fibre Reinforced Composites
What are fibre reinforced composites?
Fibre reinforced composites are materials made by combining a matrix (such as resin) with reinforcing fibres (like glass, carbon, or natural fibres) to enhance strength, stiffness, and other mechanical properties.
How do fibre orientations affect composite properties?
Fibre orientation significantly influences a composite's strength and stiffness. Aligning fibres in the direction of load application enhances the composite's ability to bear loads, while multi-directional orientations can improve strength and stiffness in multiple directions.
Can fibre reinforced composites be recycled?
Recycling of fibre reinforced composites is challenging due to their heterogeneous nature. However, methods like mechanical grinding, pyrolysis, and chemical processing are being developed and refined for effective recycling.
What are the main applications of fibre reinforced composites?
These composites are widely used in aerospace, automotive, marine, and construction industries for parts that require high strength-to-weight ratios, corrosion resistance, and durability under demanding conditions.
How do environmental factors affect fibre reinforced composites?
Environmental factors such as moisture, UV radiation, and temperature variations can degrade the matrix, impact fibre-matrix adhesion, and lead to reduced mechanical performance. Proper selection of materials and protective coatings can mitigate these effects.