Root Cause Analysis - Efficient Problem Solving
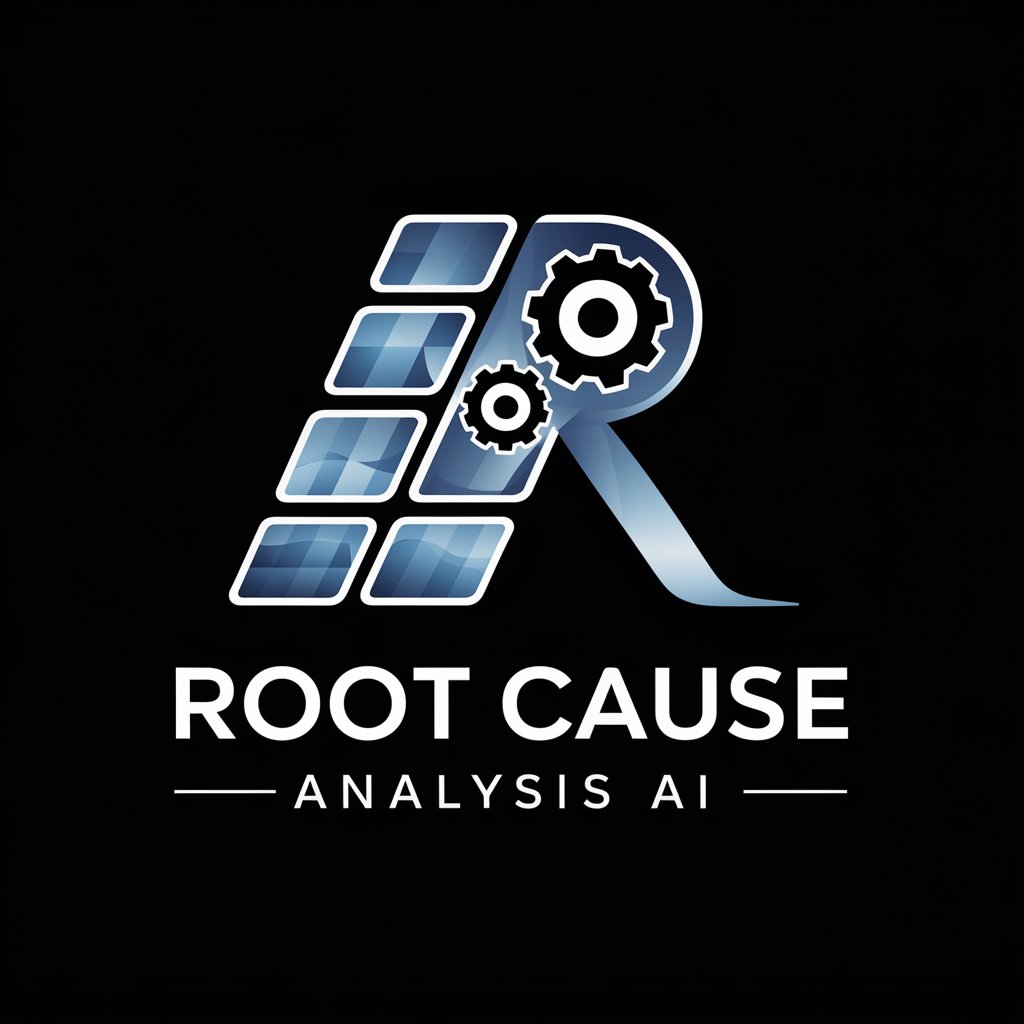
Welcome to Root Cause Analysis AI, your guide to solving manufacturing issues!
Unearth the root, fix for good.
What are the common issues faced in solar panel manufacturing?
How can we identify the root cause of a production delay?
What tools can assist in analyzing manufacturing defects?
What steps should be taken to ensure quality control in solar panel production?
Get Embed Code
Understanding Root Cause Analysis
Root Cause Analysis (RCA) is a systematic process used to identify the underlying reasons for failures or problems within a system or process. The primary goal of RCA is to determine the origin of a problem, allowing for the implementation of solutions that prevent future occurrences rather than just addressing symptoms. An example of RCA in action is in the manufacturing industry: if a production line repeatedly halts, RCA would be used to examine all aspects of the production process, from machinery operation to software systems, to determine why these stoppages are occurring. This might involve analyzing maintenance records, operator error, and component failures to identify and address the foundational issues causing the disruptions. Powered by ChatGPT-4o。
Core Functions of Root Cause Analysis
Problem Identification
Example
Identifying discrepancies in output quality in a semiconductor manufacturing process
Scenario
RCA begins by recognizing that the quality of semiconductors is below expected standards. The process might involve initial data collection through quality control metrics and interviews with the operational team to pinpoint where the failures are most frequent.
Data Collection
Example
Gathering data on machine performance and operator inputs in an automotive assembly line
Scenario
Once a problem is identified, detailed data collection follows. For instance, logging and analyzing the performance data of robotic arms on the assembly line and the corresponding operator control settings can help determine if errors are due to mechanical failure, software issues, or human error.
Cause Analysis
Example
Using fault tree analysis to investigate a power failure in a data center
Scenario
This function involves using analytical tools like fault tree analysis to trace the sequence of events leading to the power failure. By constructing a logical diagram that maps all possible causes of the failure, technicians can identify whether the issue stemmed from a hardware malfunction, software glitch, or an external power supply issue.
Solution Implementation
Example
Implementing a new training program for operators after identifying frequent user errors in machinery handling
Scenario
After identifying the root causes, effective solutions are implemented to prevent recurrence. In this case, if frequent operator errors are detected, a targeted training program can be developed to enhance operator skills and knowledge, thereby reducing future errors and improving overall productivity.
Target User Groups for Root Cause Analysis
Manufacturing Sector Professionals
Engineers, quality control managers, and maintenance teams in the manufacturing sector benefit from RCA to improve product quality, optimize processes, and reduce costs due to failures.
Healthcare Administrators
Healthcare administrators use RCA to investigate incidents like patient safety breaches or equipment failures, aiming to enhance care quality and operational safety.
IT and Network Administrators
These professionals use RCA to troubleshoot system outages or breaches in network security, ensuring reliability and integrity of IT services.
How to Utilize Root Cause Analysis Effectively
Initiate a Trial
Start by exploring yeschat.ai for an obligation-free trial, no account creation or ChatGPT Plus subscription necessary.
Identify the Problem
Clearly define the problem you're experiencing. Document all symptoms and relevant data to ensure a comprehensive understanding.
Collect Data
Gather detailed information related to the problem. This includes operational data, logs, and firsthand observations.
Analyze Data
Use Root Cause Analysis tools to dissect the collected data. Look for patterns or anomalies that could indicate underlying causes.
Implement Solutions
Based on the analysis, develop and apply solutions. Monitor the results closely to ensure the problem is resolved.
Try other advanced and practical GPTs
Root Cause Investigator
Discover What's Really Going On
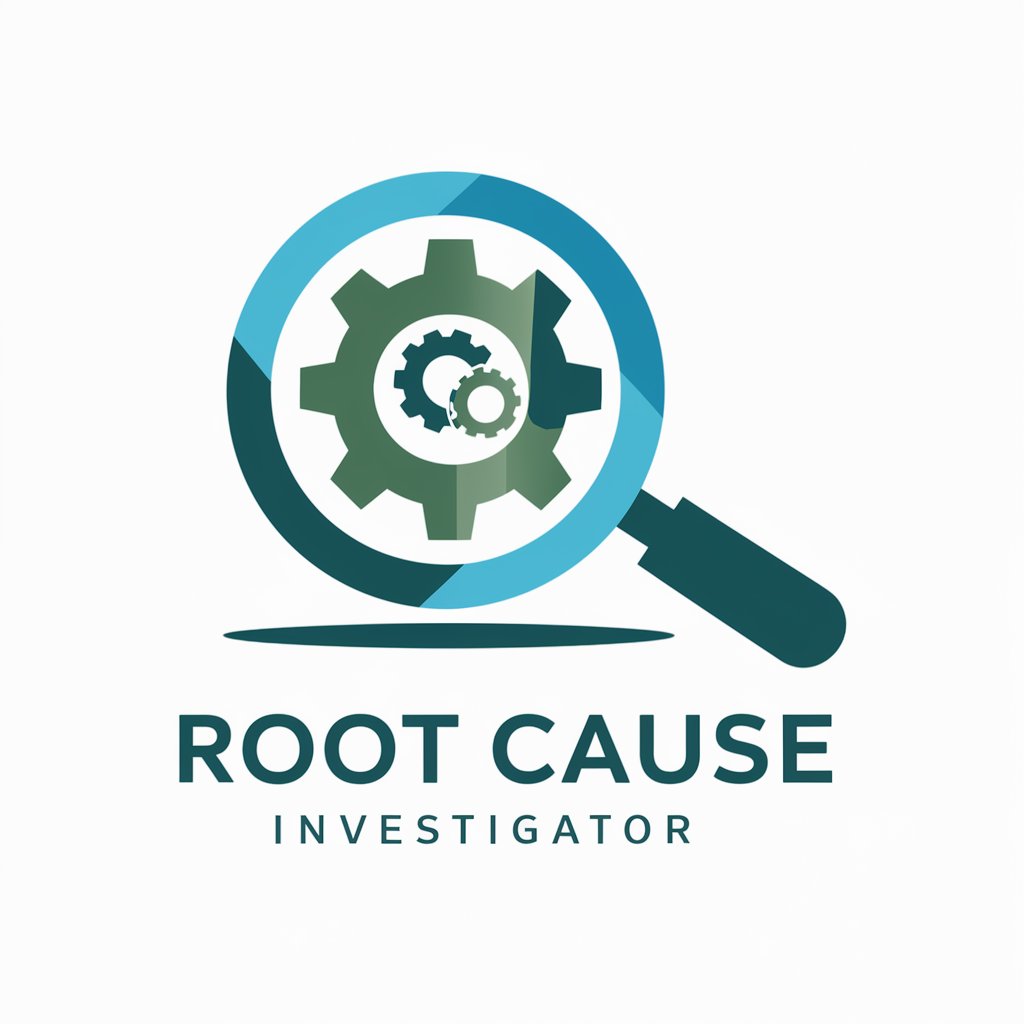
Root Cause Detective
Uncover Causes with AI Precision
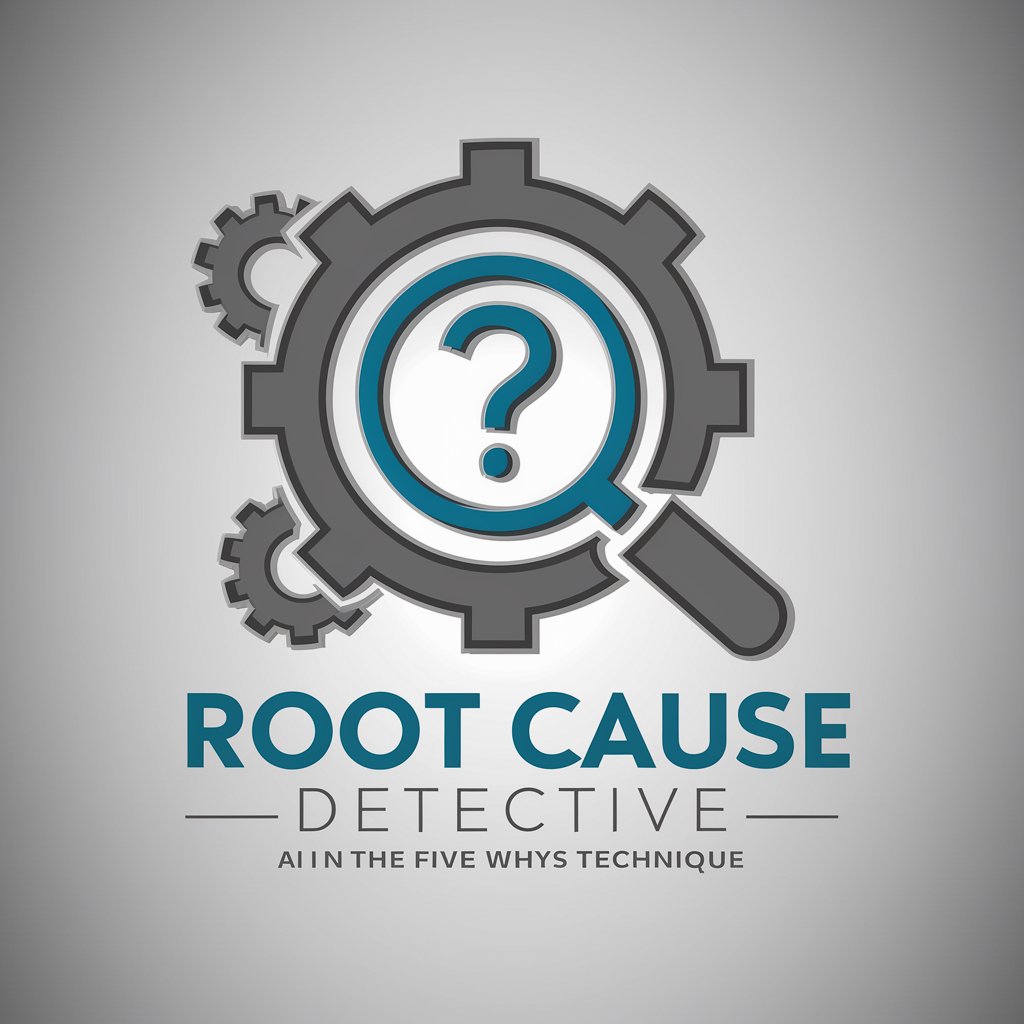
Code With Cause
AI-Powered Interactive Guidance and Learning

Review & Refine GPT
Empowering Your Words with AI Insight
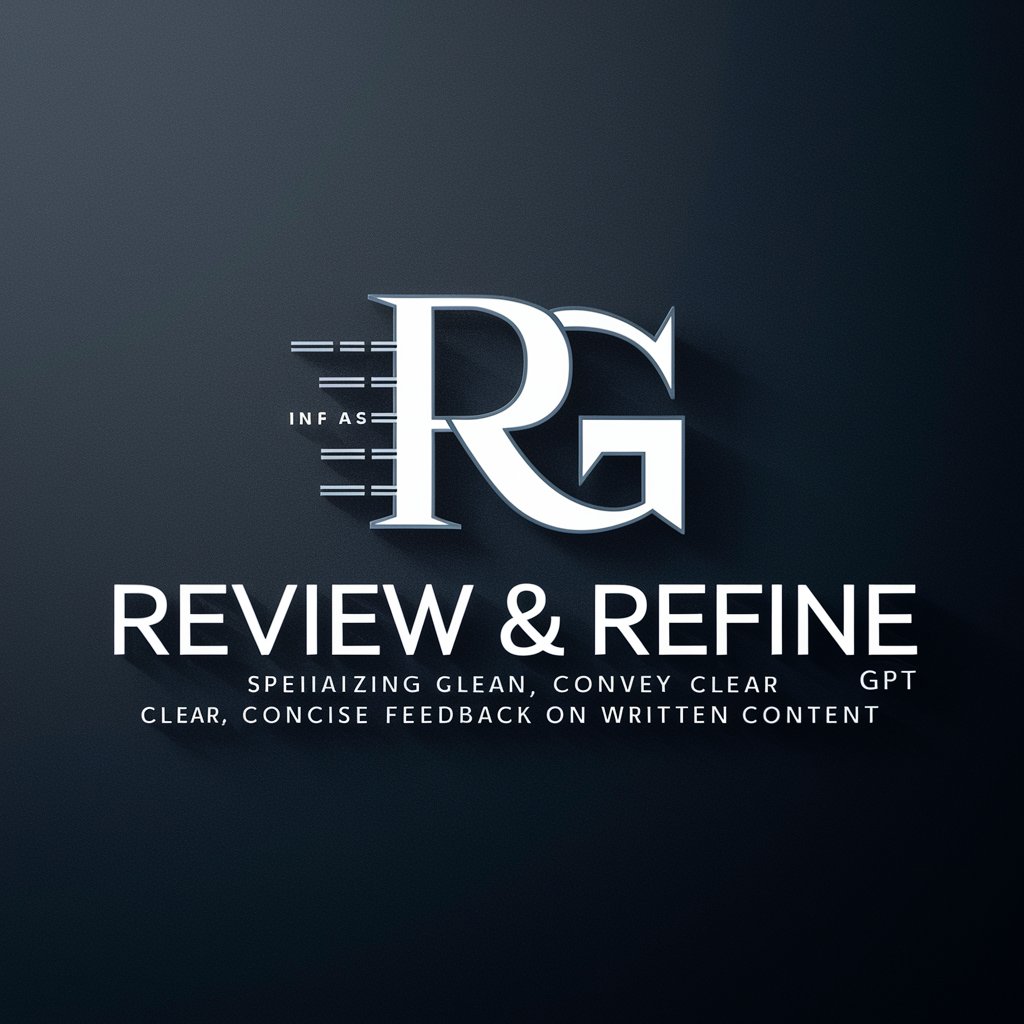
Investment Analyst
Decipher Market Trends with AI-Powered Insights
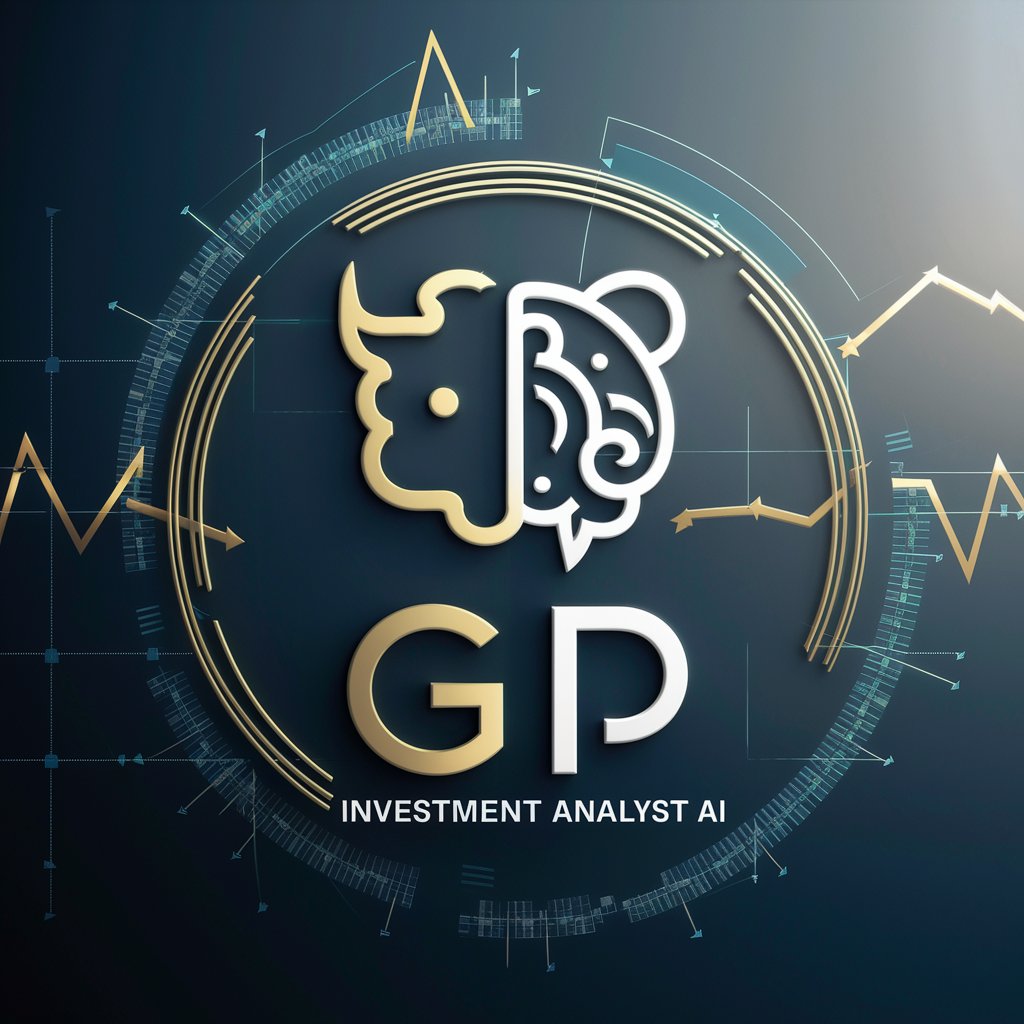
Investment Assistant
AI-powered investment research and strategy tool

Root Cause Explorer
Uncover the core, power your solutions

Crypto Cause Effect Assistant
Unraveling Crypto Trends with AI
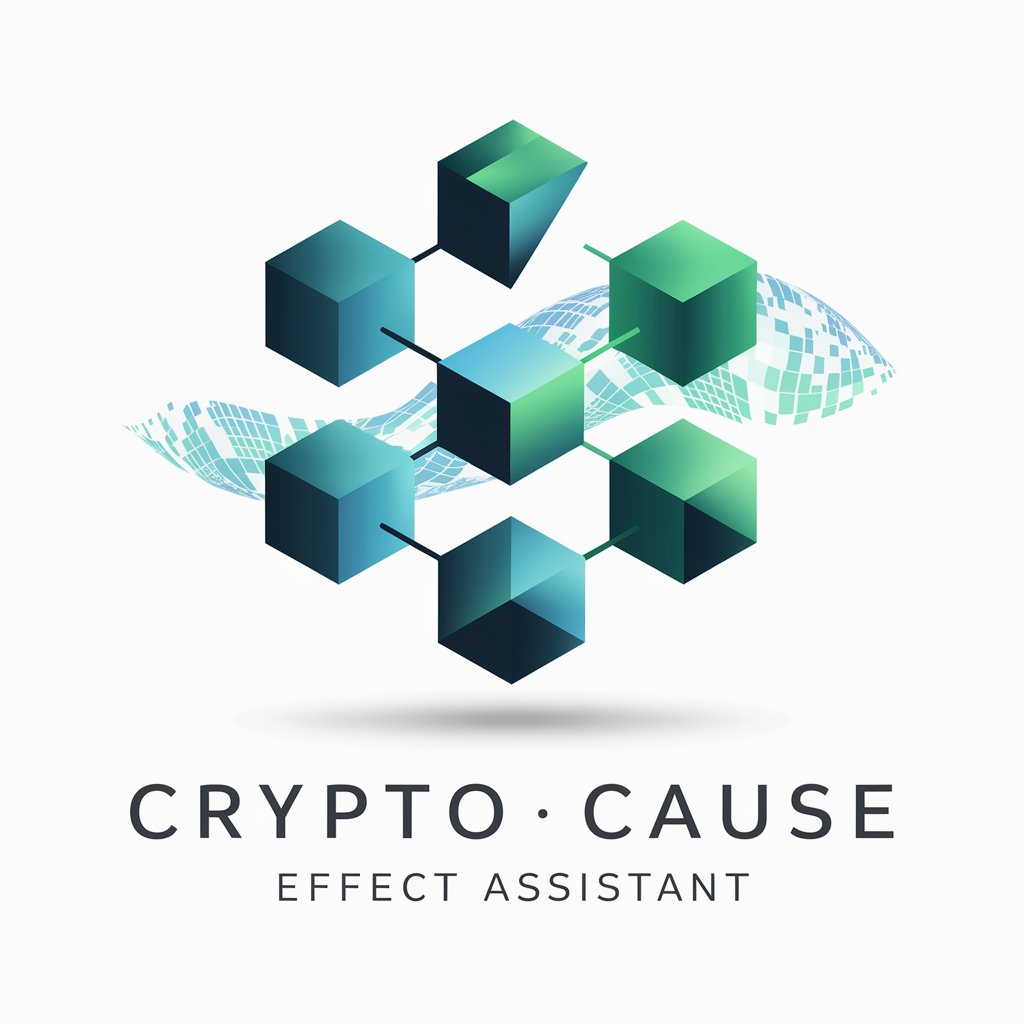
Character Assistant
Empower Your Work with AI

AI Writer - Cold Email Assistant
Empowering your outreach with AI

Newsletter Writer
Craft Your Newsletter with AI
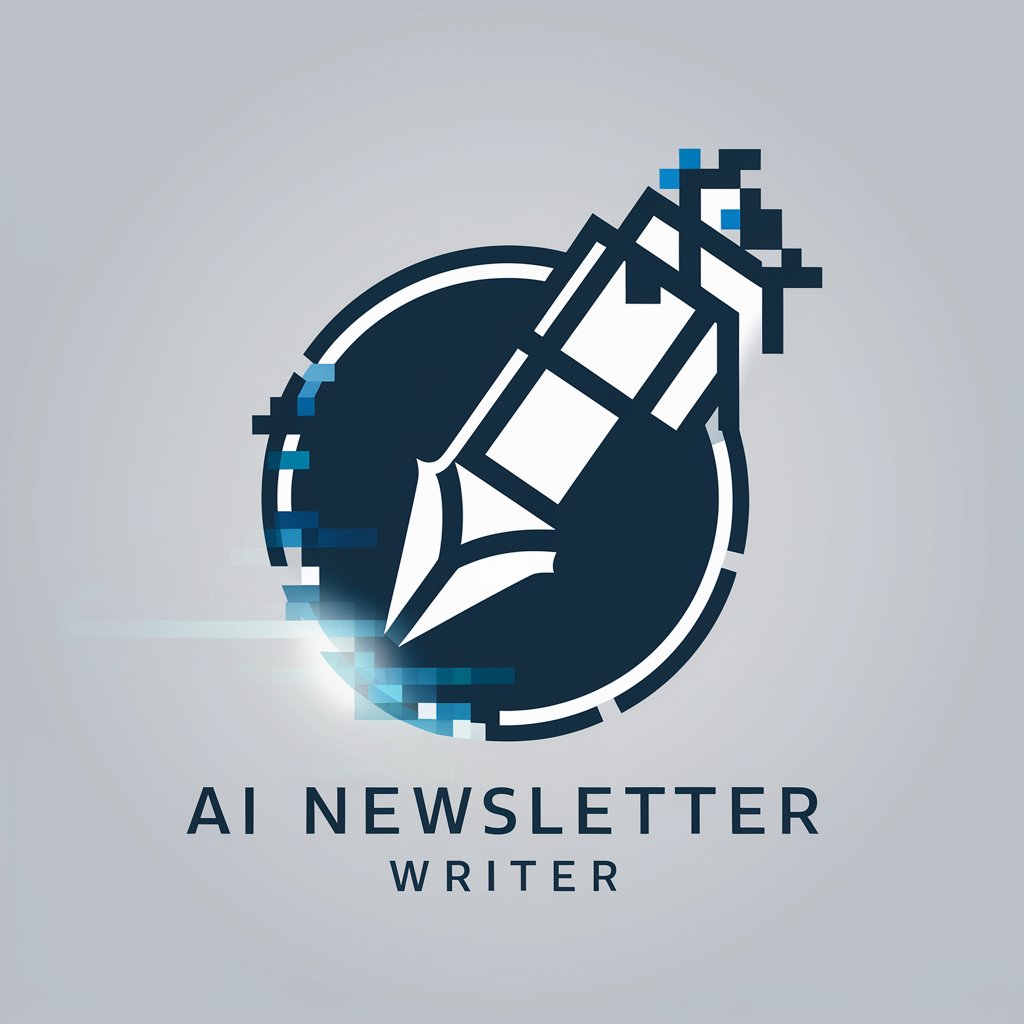
MailGPT
Streamlining email communication with AI
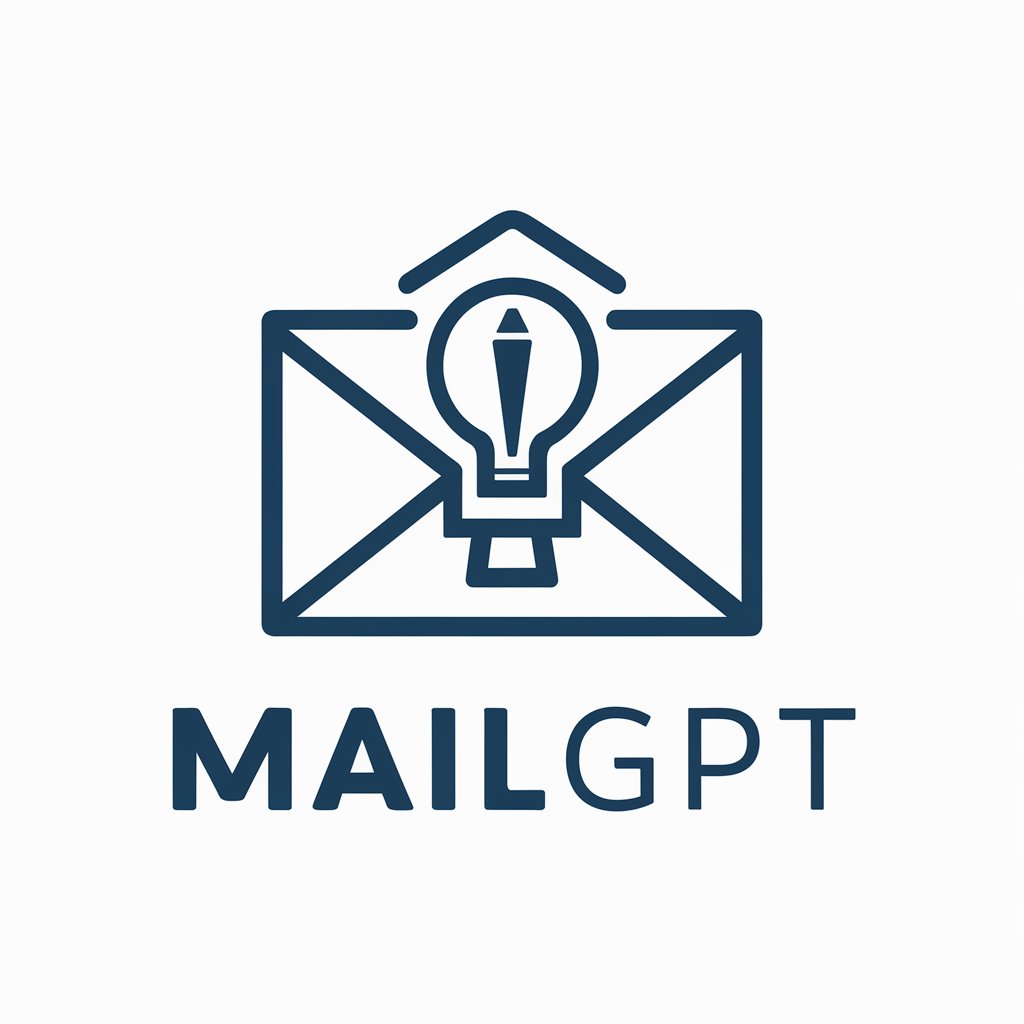
In-depth Q&A on Root Cause Analysis
What is Root Cause Analysis?
Root Cause Analysis (RCA) is a systematic process used for identifying the fundamental causes of problems or events. It aims to address the root causes rather than merely treating the symptoms, ensuring that issues do not recur.
Why is RCA important in manufacturing?
In manufacturing, RCA is crucial for minimizing downtime, improving production efficiency, and enhancing product quality. It helps identify and correct underlying issues that could lead to significant financial losses.
Can RCA be applied in software development?
Yes, RCA is highly beneficial in software development. It's used to troubleshoot bugs, failures, and performance issues, ensuring that the same problems are not repeatedly fixed on the surface level only.
What tools are used in RCA?
RCA employs various tools such as the 5 Whys, Fishbone (Ishikawa) Diagram, Pareto Analysis, and Failure Mode and Effects Analysis (FMEA) to systematically identify root causes.
How can I ensure the effectiveness of RCA?
The effectiveness of RCA depends on accurate data collection, a thorough analysis, involving cross-functional teams for diverse insights, and implementing corrective actions that are closely monitored for effectiveness.