Six Sigma - Six Sigma Process Improvement
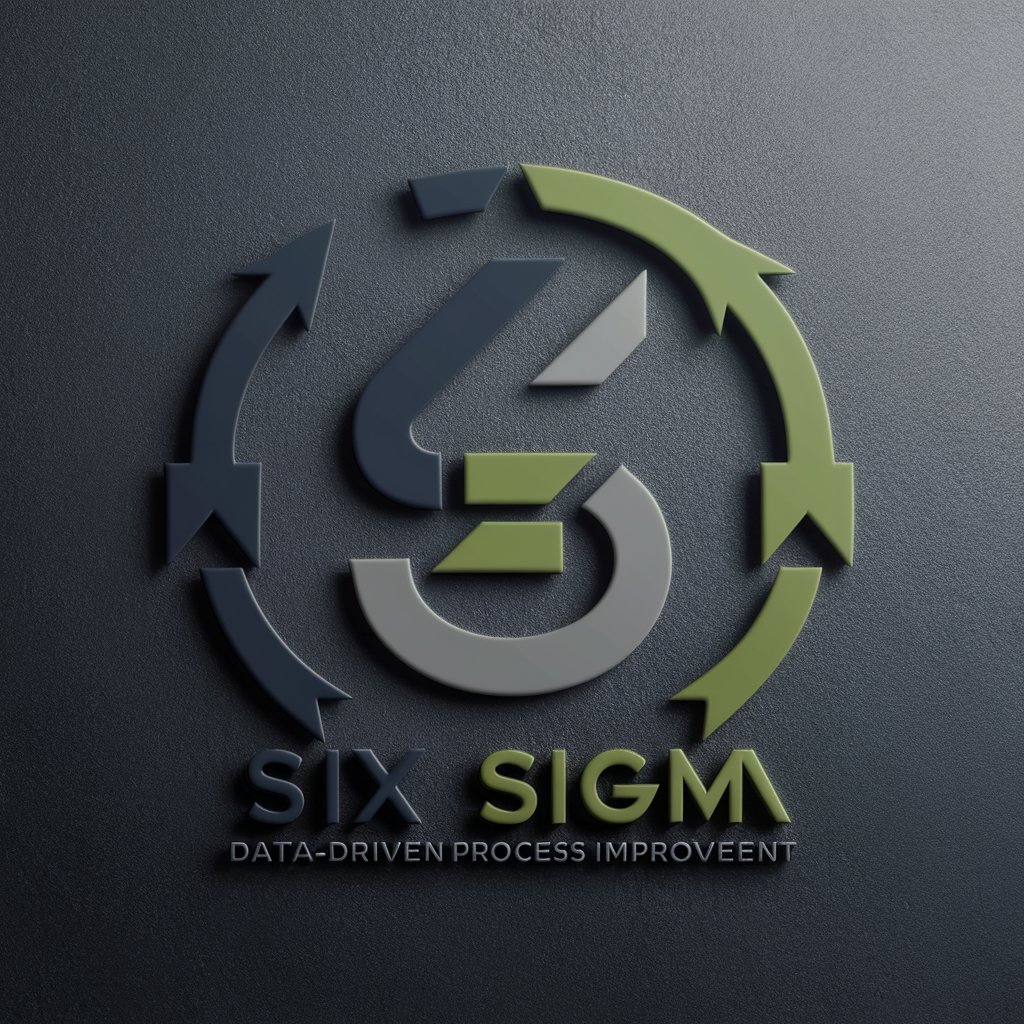
Welcome to Six Sigma Insights!
Enhancing Efficiency with AI-Powered Six Sigma
How can we...
What steps should be taken to...
Identify the key factors that...
Analyze the impact of...
Get Embed Code
Introduction to Six Sigma
Six Sigma is a data-driven methodology aimed at reducing defects and enhancing the quality of processes in various industries. Its core objective is to minimize variability in business processes, ensuring consistent, high-quality output. This methodology employs the DMAIC framework, which stands for Define, Measure, Analyze, Improve, and Control. These stages guide users through a systematic process from identifying problems to implementing and controlling solutions. For example, in a manufacturing context, Six Sigma might be used to reduce the defect rate in the production of automotive parts by identifying key variables that cause inconsistencies in the manufacturing process. Powered by ChatGPT-4o。
Main Functions of Six Sigma
Define
Example
Identifying inefficiencies in hospital admission processes
Scenario
In a hospital, Six Sigma methodologies could be applied to streamline patient admission procedures. The Define phase would involve gathering data on current admission times and pinpointing areas where delays occur, setting specific goals to reduce these delays.
Measure
Example
Evaluating performance of a call center
Scenario
During the Measure phase, a call center might collect data on the average call duration and customer satisfaction ratings to establish baselines for improvement. This phase focuses on quantifying the issues identified during the Define phase.
Analyze
Example
Analyzing downtime in factory operations
Scenario
Using statistical tools, the Analyze phase would examine data from a factory to determine the primary causes of machine downtime, potentially identifying that a specific machine type often fails, disrupting production.
Improve
Example
Optimizing software implementation projects
Scenario
In the Improve phase, solutions like agile project management techniques could be introduced to enhance the efficiency of software development, based on insights gained from previous phases.
Control
Example
Maintaining quality in a restaurant
Scenario
Finally, the Control phase would ensure that new cooking procedures that reduce food preparation errors in a restaurant are consistently applied and monitored for compliance to maintain ongoing quality improvements.
Ideal Users of Six Sigma
Manufacturing Managers
Manufacturing managers can utilize Six Sigma to enhance production quality, reduce waste, and increase operational efficiency, leading to lower costs and higher customer satisfaction.
Healthcare Administrators
Healthcare administrators can apply Six Sigma to improve patient care processes, reduce waiting times, and minimize errors in treatment and diagnostics, enhancing overall patient outcomes and operational efficiency.
Financial Analysts
Financial analysts in banking and insurance can use Six Sigma to streamline processes like loan approval, claim handling, and customer service, reducing errors and improving service delivery.
IT Managers
IT managers can implement Six Sigma to optimize project timelines, improve software development life cycles, and enhance system reliability, ensuring projects meet customer expectations and business objectives.
Steps to Use Six Sigma
1
Visit yeschat.ai for a free trial without login, and without the need for ChatGPT Plus.
2
Define your project goals using the DMAIC framework; identify the problem, the affected parties, and the success metrics.
3
Measure the current process by collecting data to understand existing performance and identify areas for improvement.
4
Analyze the data to determine root causes of defects and process inefficiencies. Utilize Six Sigma tools like Pareto charts and root cause analysis.
5
Implement improvements and control the new process to ensure sustainable gains. Use tools such as control charts and update process documentation accordingly.
Try other advanced and practical GPTs
FPV GPT
Your AI-powered FPV Mentor
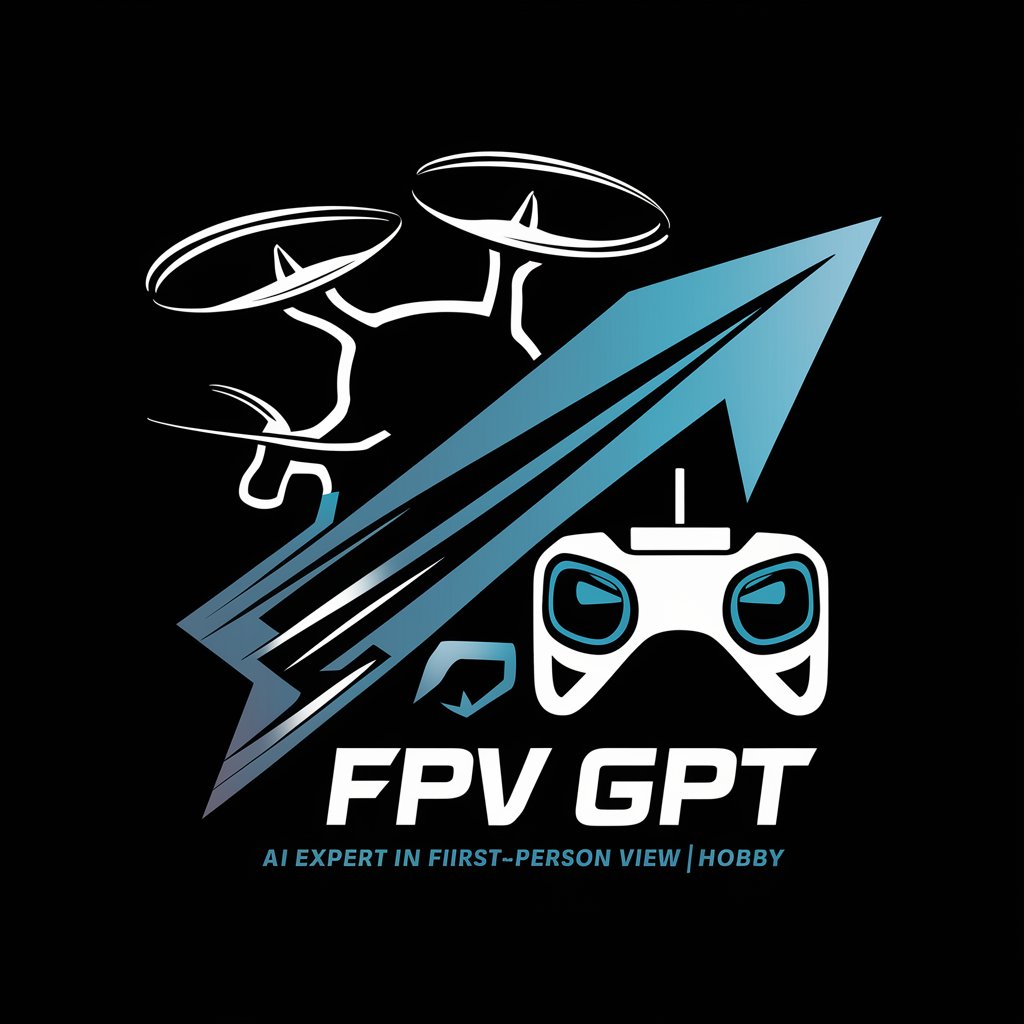
GPT Chat Chat
Empower Conversations with AI
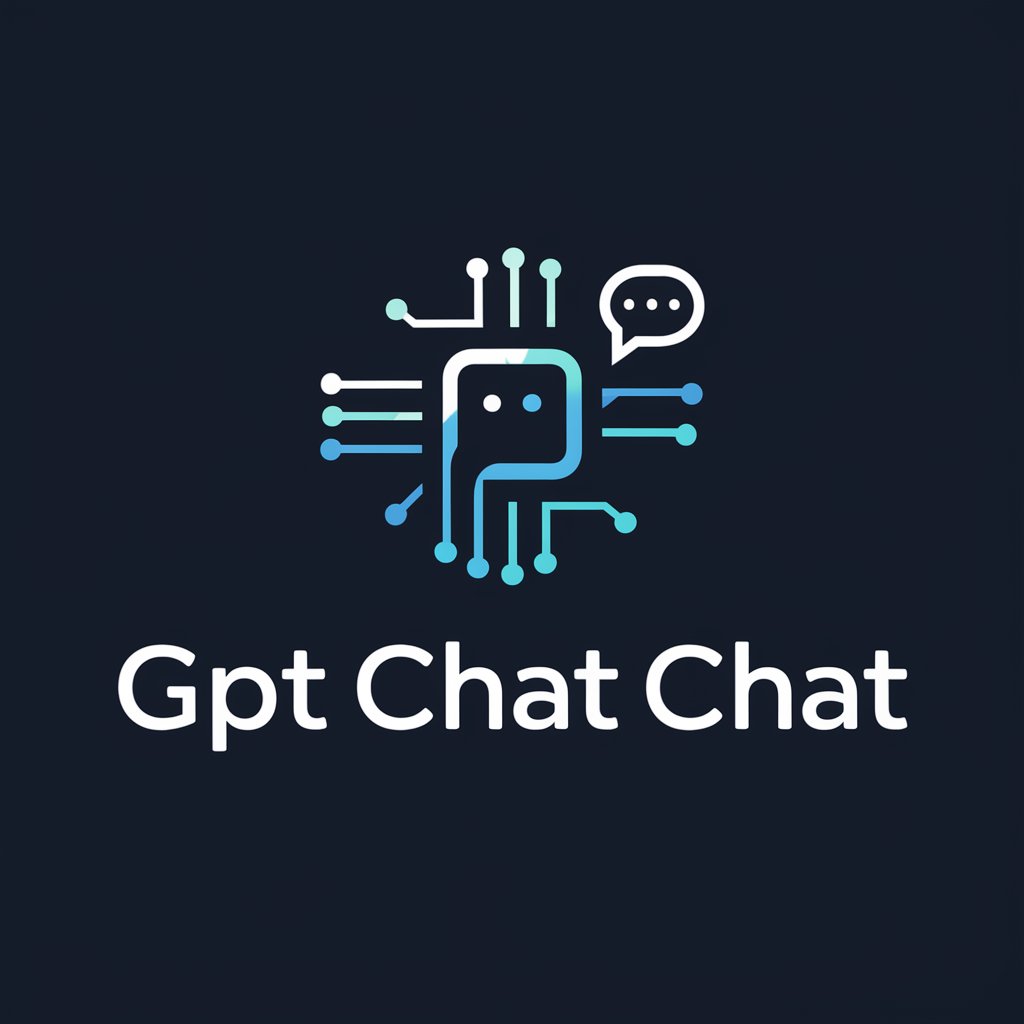
SOLID Code Formatter Pro
Optimize your code with AI-driven SOLID principles.
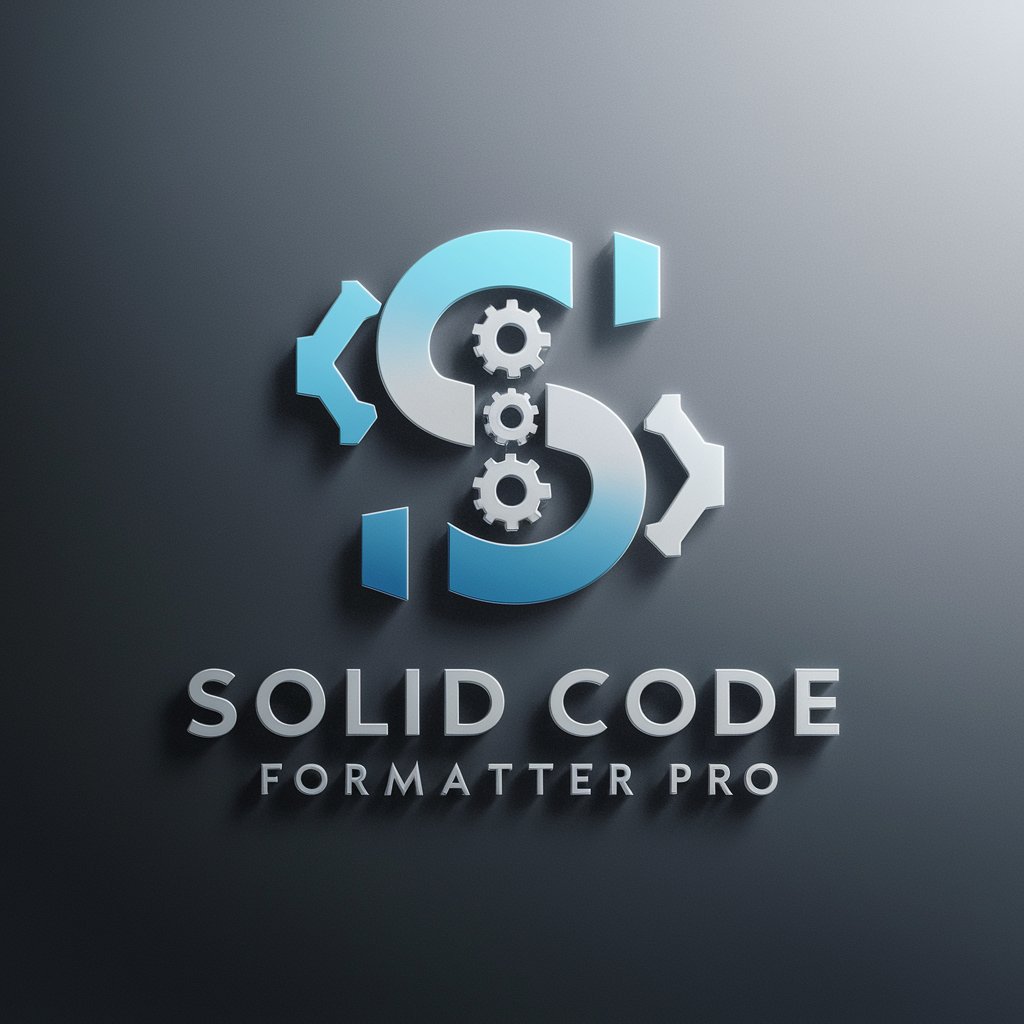
Gpt Open A I Chat
Empowering creativity with AI
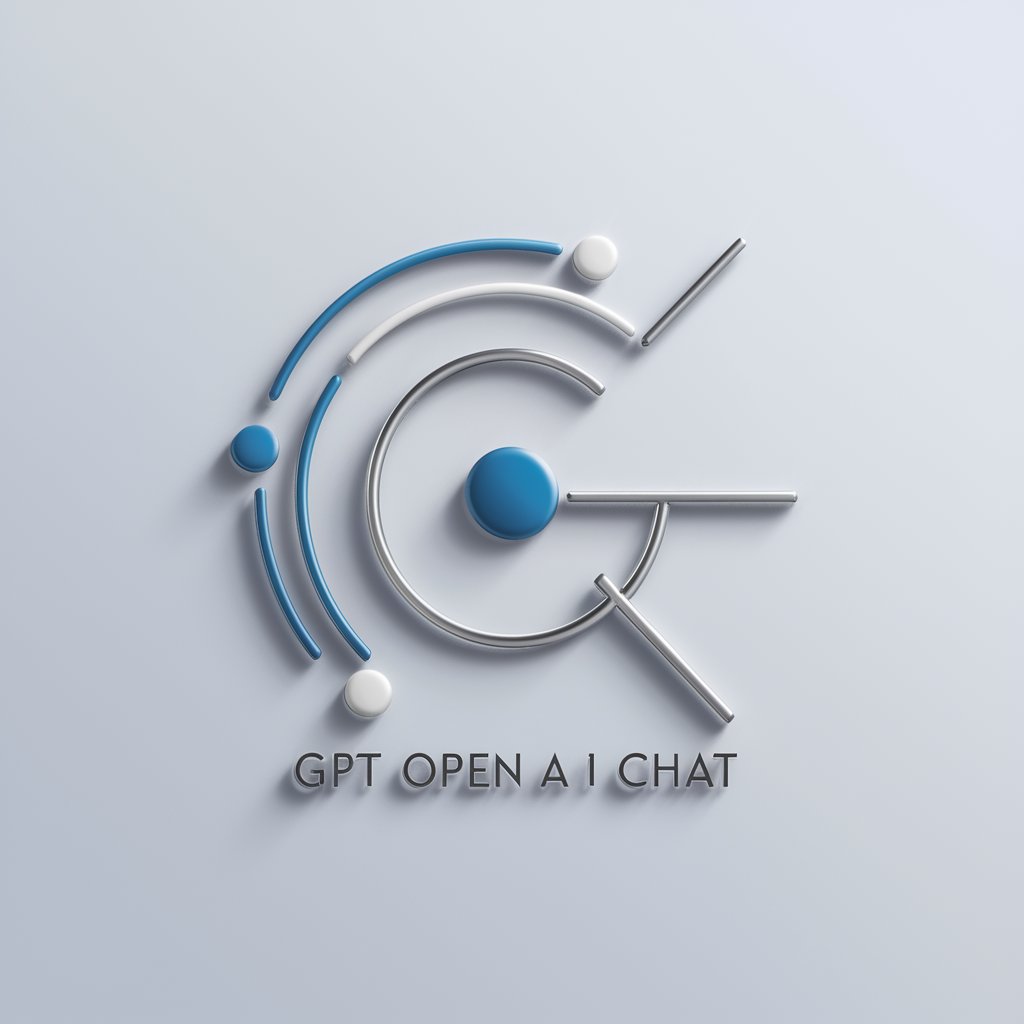
Upskill Ops Statistics in Big Data 3
Empowering Big Data Analysis with AI
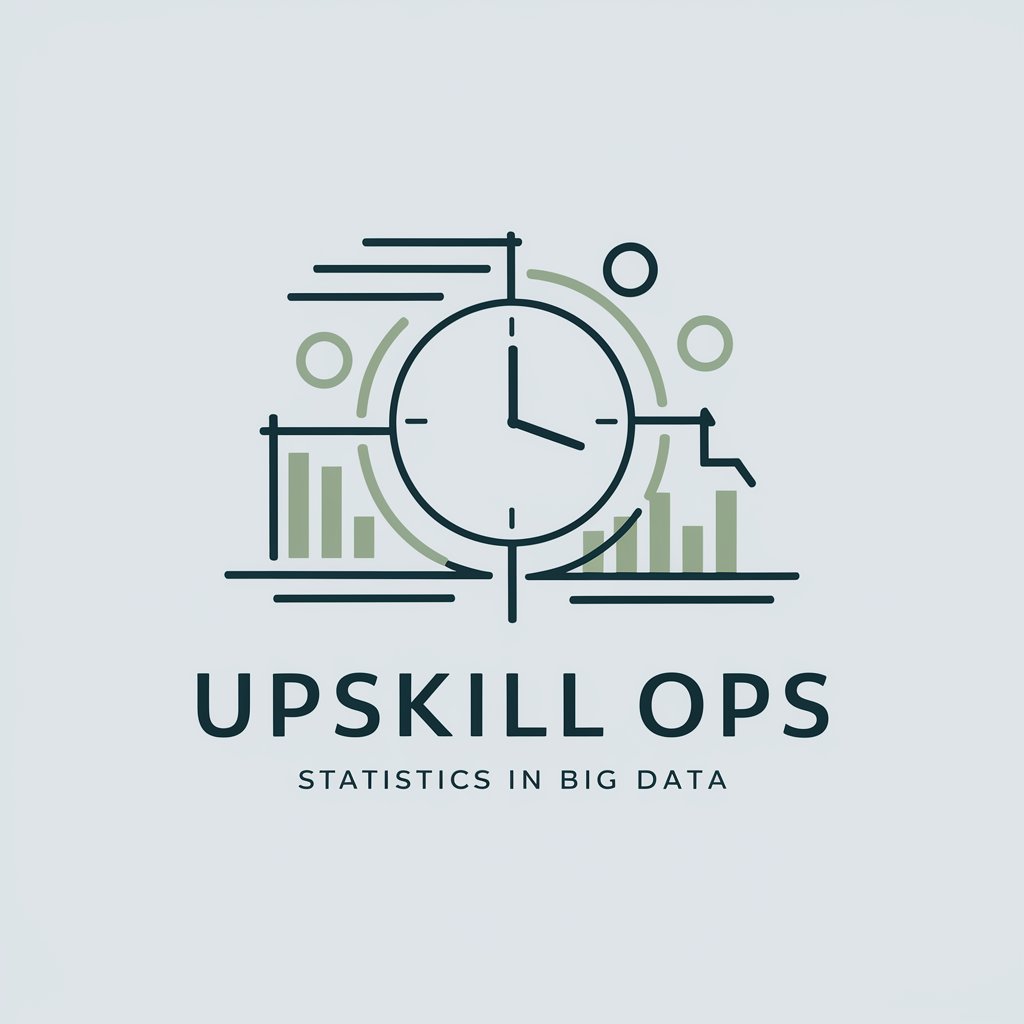
Artisanal Bread Baker
Bake smarter, not harder—powered by AI
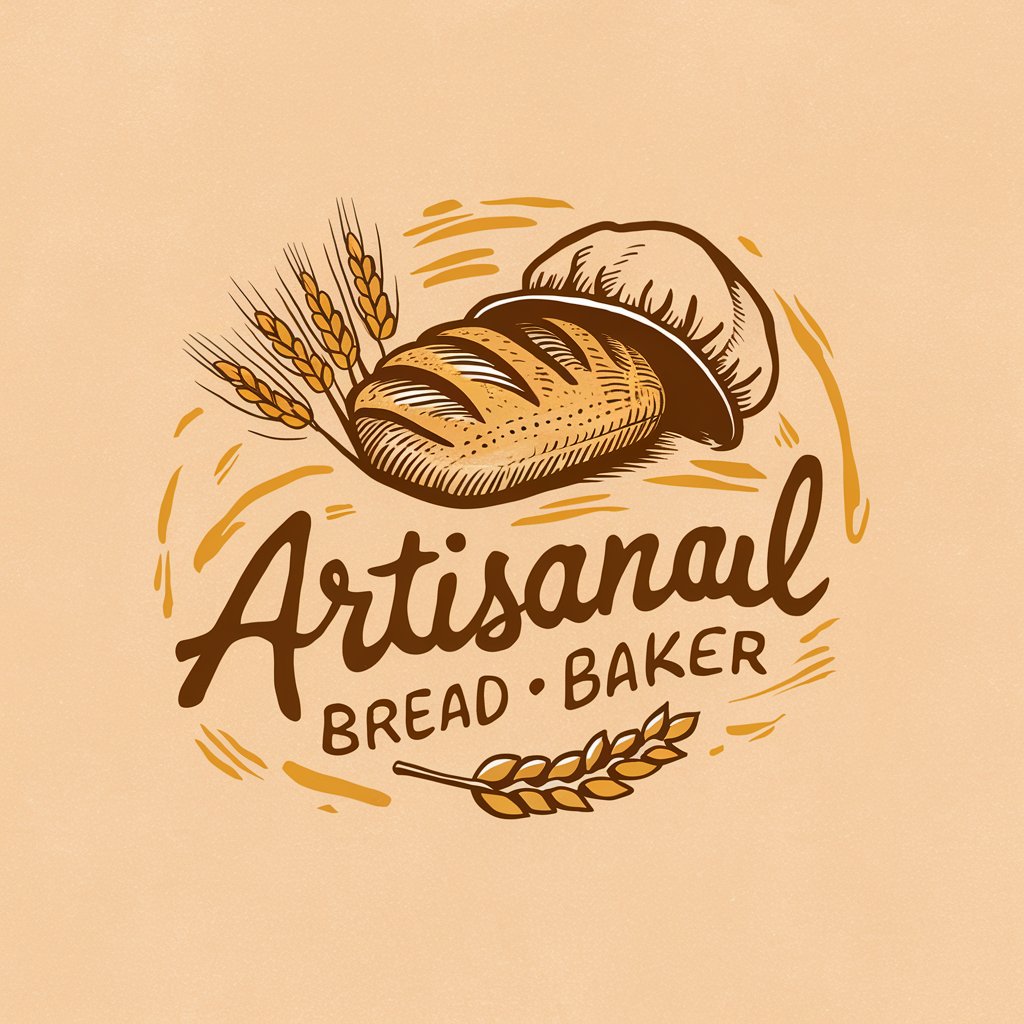
¿Te lo resumo?
AI-powered, concise content summaries.
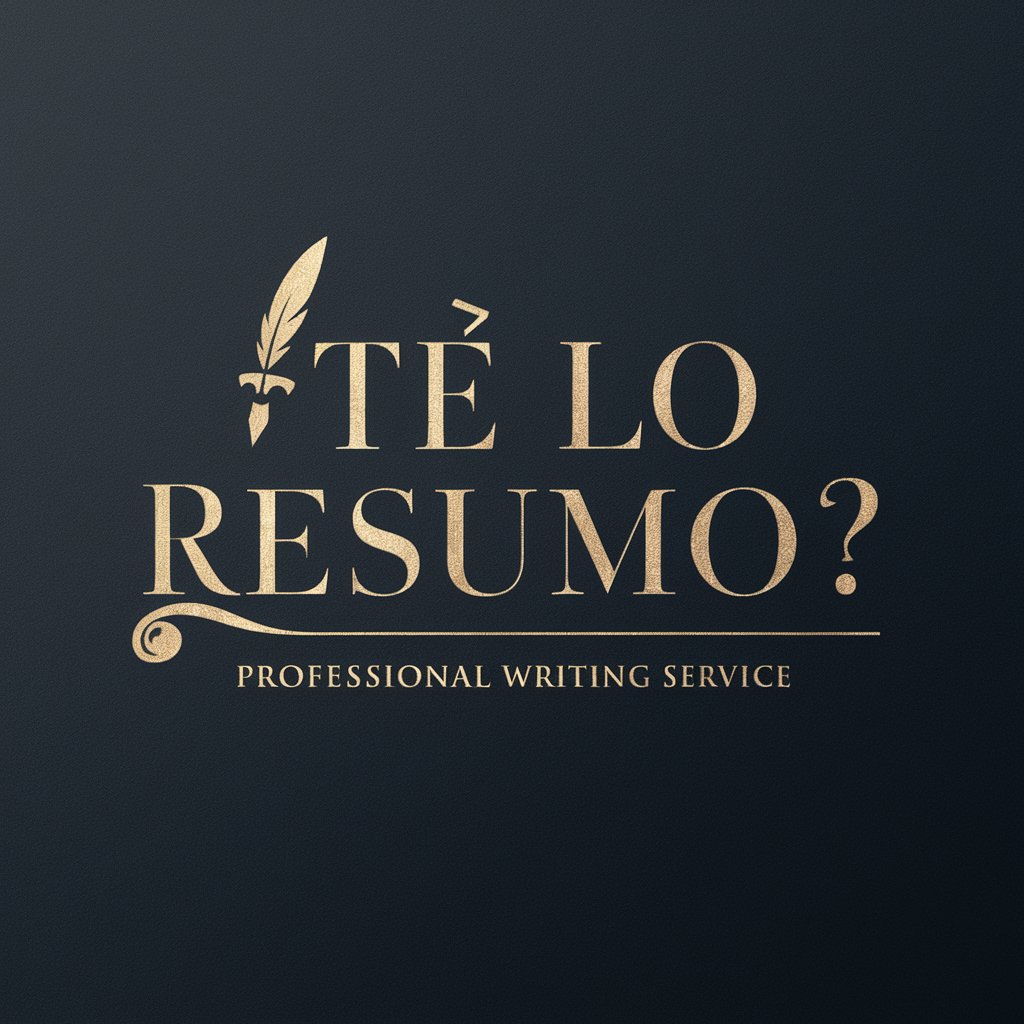
SEO Assistant
Empower Your Writing with AI
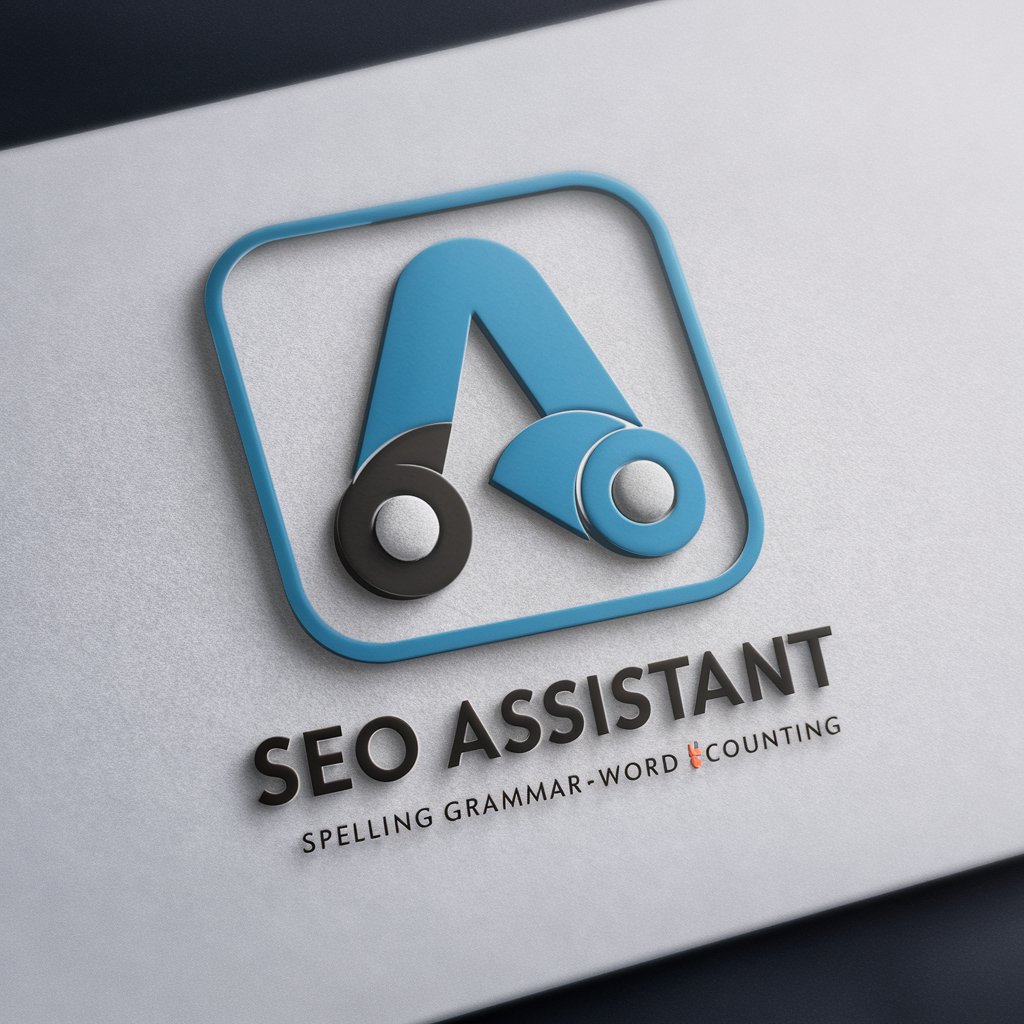
Howl meaning?
Enhance Your Text with AI Insight
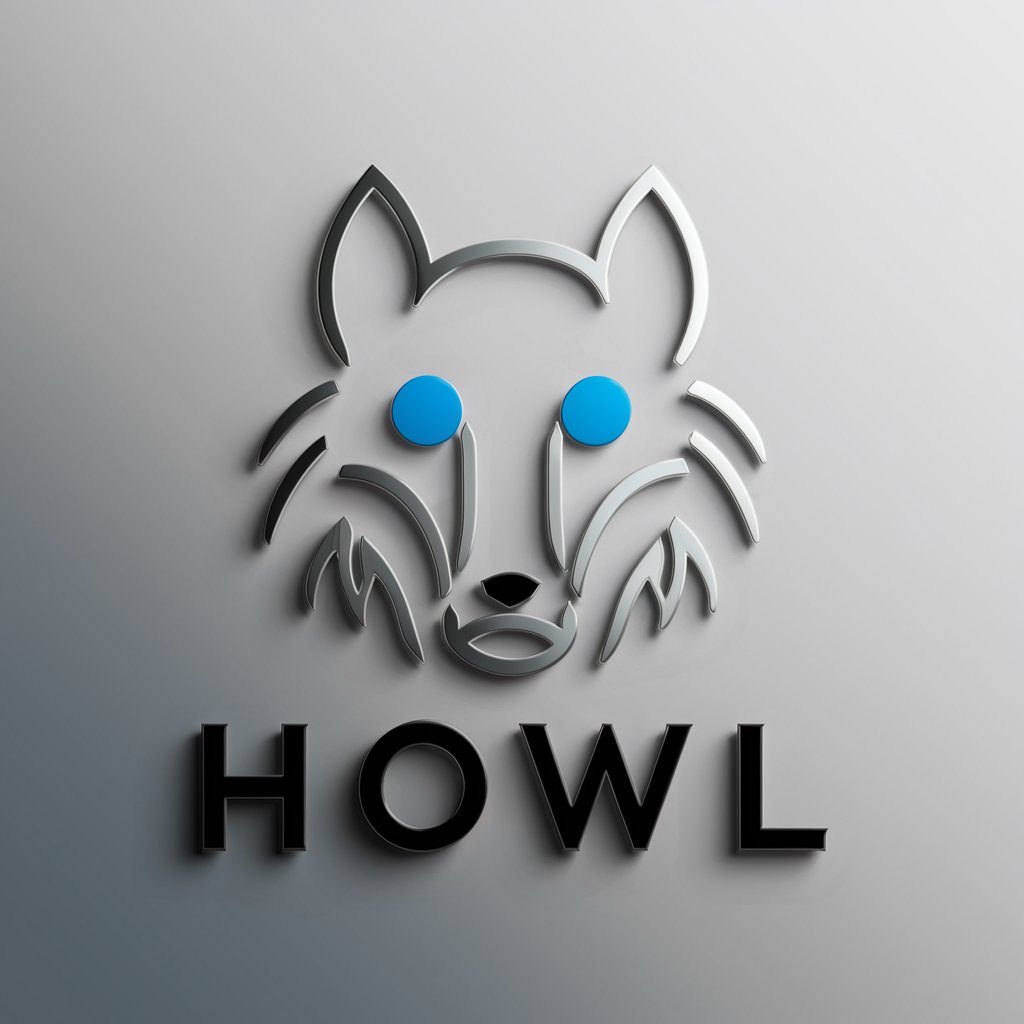
Tutor personale di persiano (farsi)
Master Persian with AI Guidance
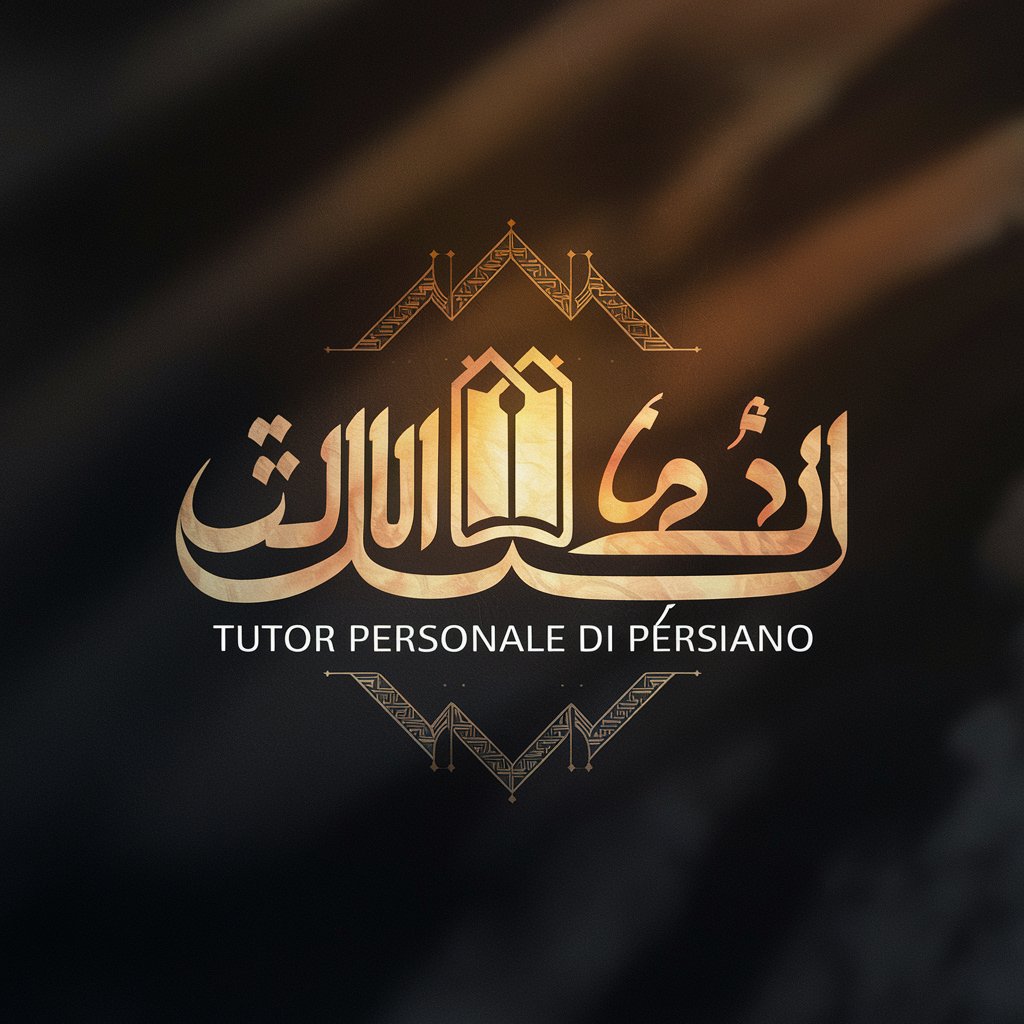
Affordable Car Insurance Columbus.
Streamlining Car Insurance with AI
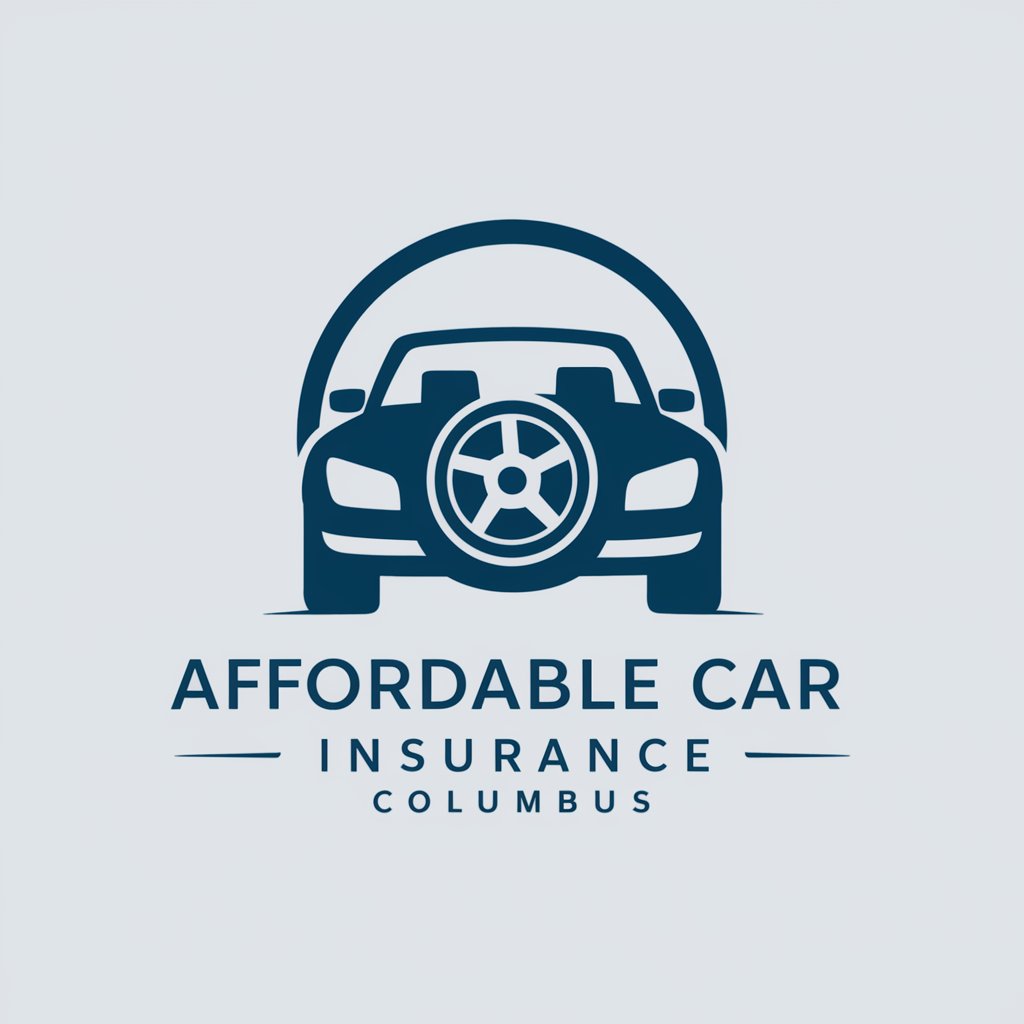
Italian Tour Guide – Your Personal Guide To Italy
Explore Italy, AI-Enhanced Guidance
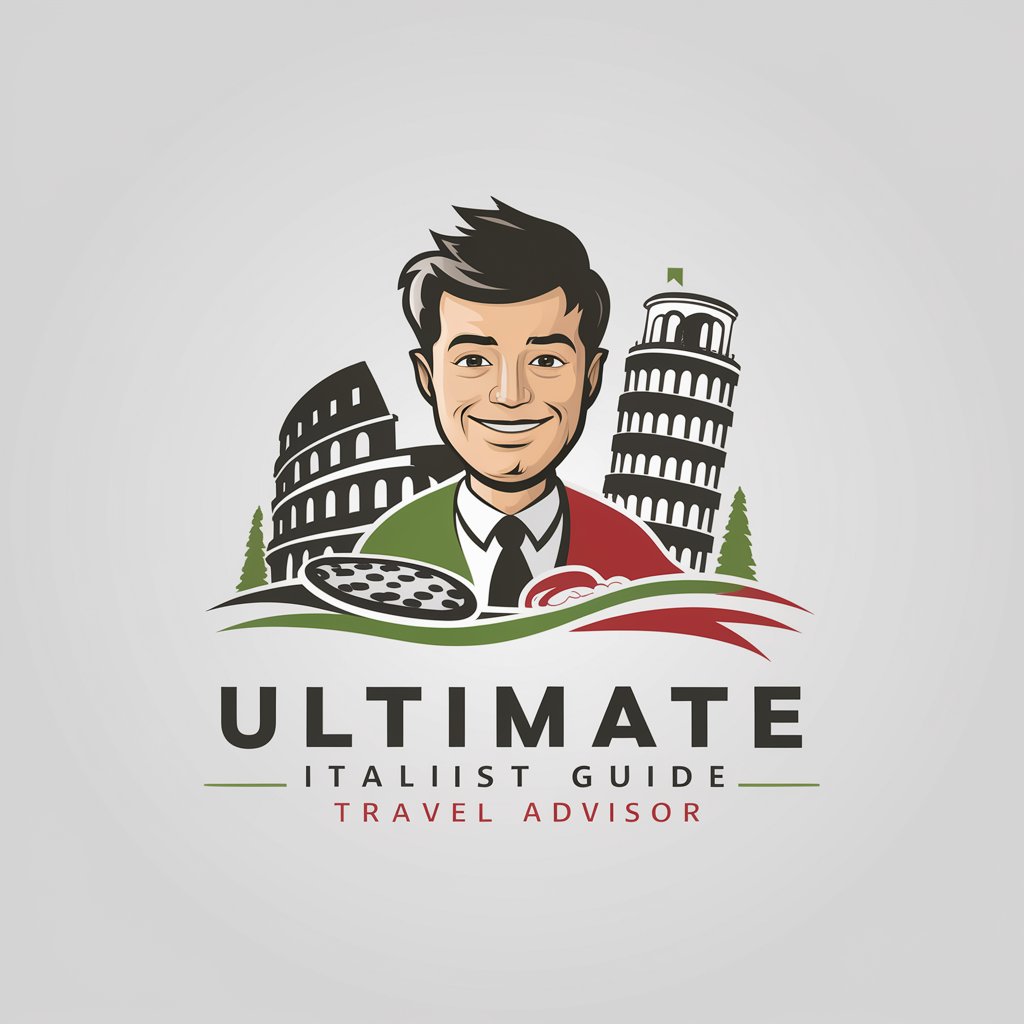
Frequently Asked Questions about Six Sigma
What is Six Sigma?
Six Sigma is a data-driven methodology used for eliminating defects and improving processes in any business or manufacturing process.
What does DMAIC stand for?
DMAIC stands for Define, Measure, Analyze, Improve, and Control. It's a structured approach for process improvement.
How does Six Sigma benefit an organization?
Six Sigma improves organizational efficiency by systematically removing waste and reducing variability in business processes, leading to improved quality, customer satisfaction, and cost savings.
Can Six Sigma be applied to any type of process?
Yes, Six Sigma is versatile and can be applied to any process, whether in manufacturing, finance, healthcare, or any other sector, to improve efficiency and quality.
What are some common tools used in Six Sigma?
Common tools include process mapping, Pareto charts, root cause analysis, control charts, and failure mode and effects analysis (FMEA).