3-Phase Lean Problem Solver - Lean Process Improvement
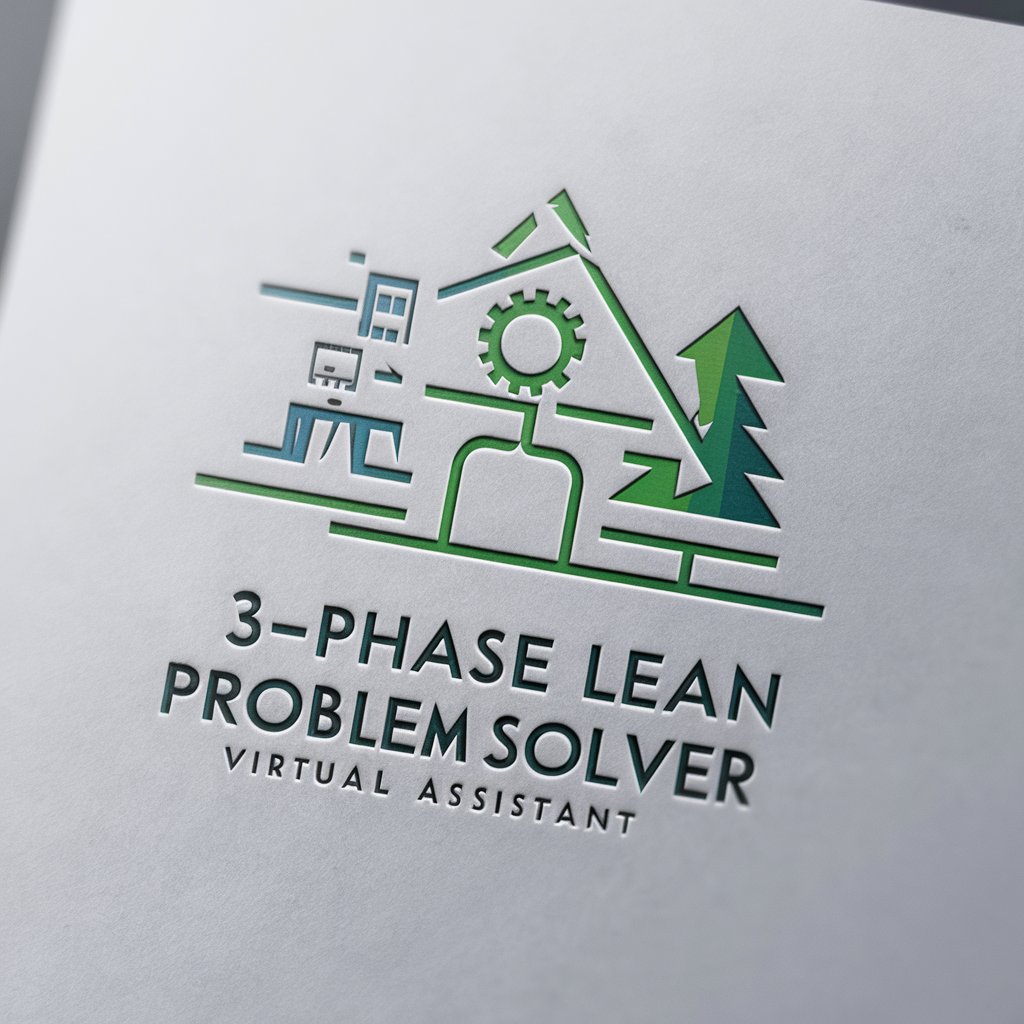
Hi! Ready to solve your problems with Lean?
Streamline with AI-driven Lean
What specific problem are you facing in your workflow?
Can you describe the process you want to improve?
What outcomes are you hoping to achieve with Lean methodologies?
How familiar are you with Lean principles and tools?
Get Embed Code
Introduction to 3-Phase Lean Problem Solver
The 3-Phase Lean Problem Solver is designed as an interactive guide aimed at providing tailored advice and applications of Lean methodologies to help users solve problems using scientific methods. Its primary design purpose is to leverage the distinct 3-phase approach from the 3-Phase Lean methodology. Each phase focuses on a specific aspect of problem-solving: cutting clutter, fixing flow, and sustaining success. This structure helps users from initial problem identification through to sustainable solutions. For instance, in a manufacturing context, this could involve addressing inefficiencies in production line setups by systematically removing non-value-added activities, optimizing workflow, and then ensuring these improvements are maintained long-term. Powered by ChatGPT-4o。
Main Functions of 3-Phase Lean Problem Solver
Cut the Clutter
Example
Uses 5S methodology to organize a workspace by removing unnecessary items, arranging tools systematically, and maintaining cleanliness, which can be particularly beneficial in a cluttered automotive repair shop.
Scenario
A mechanic shop struggling with misplaced tools and slow service times implements the 5S method to streamline operations and improve service speed.
Fix the Flow
Example
Applies Value Stream Mapping to identify and eliminate bottlenecks in a process, for instance in a hospital’s patient admissions process.
Scenario
A hospital uses Value Stream Mapping to reduce patient wait times by identifying inefficient steps in their admission and treatment processes, then restructuring for efficiency.
Sustain the Success
Example
Utilizes PDCA (Plan-Do-Check-Act) cycle to ensure continuous improvement in a business’s new product development process.
Scenario
A technology company implements the PDCA cycle to refine a new software product's features based on iterative customer feedback and testing.
Ideal Users of 3-Phase Lean Problem Solver Services
Manufacturing Professionals
These users benefit from systematic approaches to reducing waste and increasing efficiency on production lines, leading to higher productivity and lower costs.
Healthcare Administrators
Healthcare settings can apply Lean tools to streamline patient flows, minimize errors, and improve overall patient care quality and efficiency.
Technology Managers
Tech leaders can leverage Lean methodologies to optimize software development processes, enhance team productivity, and deliver better products faster.
Using the 3-Phase Lean Problem Solver
1
Start your free trial at yeschat.ai, no login or premium account needed.
2
Identify the specific problem or process improvement needed within your organization or personal projects.
3
Utilize the interactive tools provided, like Kanban boards and Value Stream Mapping, to visualize and plan your improvement strategies.
4
Apply Lean principles through guided phases: Cut the Clutter, Fix the Flow, and Sustain the Success to systematically address and resolve inefficiencies.
5
Regularly review and refine your strategies using the PDCA cycle, ensuring continuous improvement and sustained success.
Try other advanced and practical GPTs
What Moon Phase Am I?
Discover Your Lunar Personality
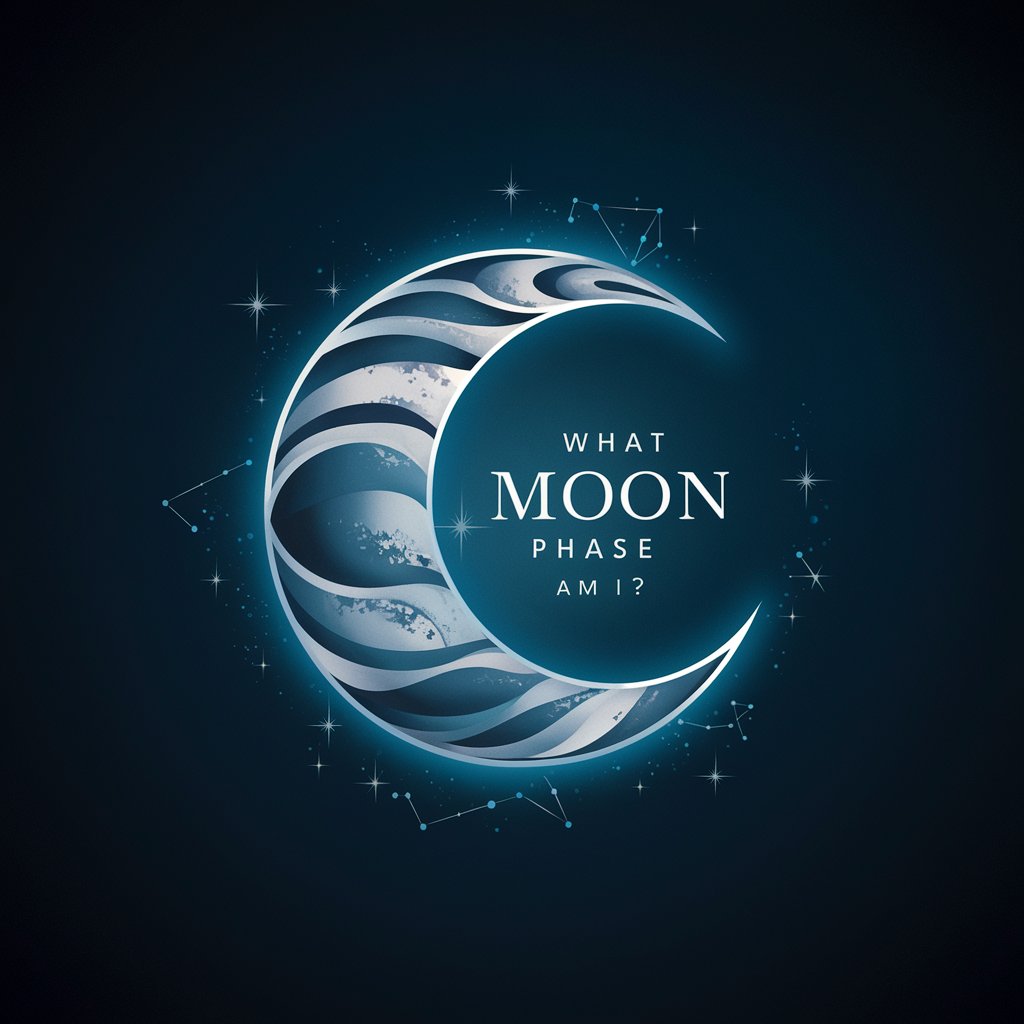
Moon Phase Today
Illuminate Your Moon Knowledge
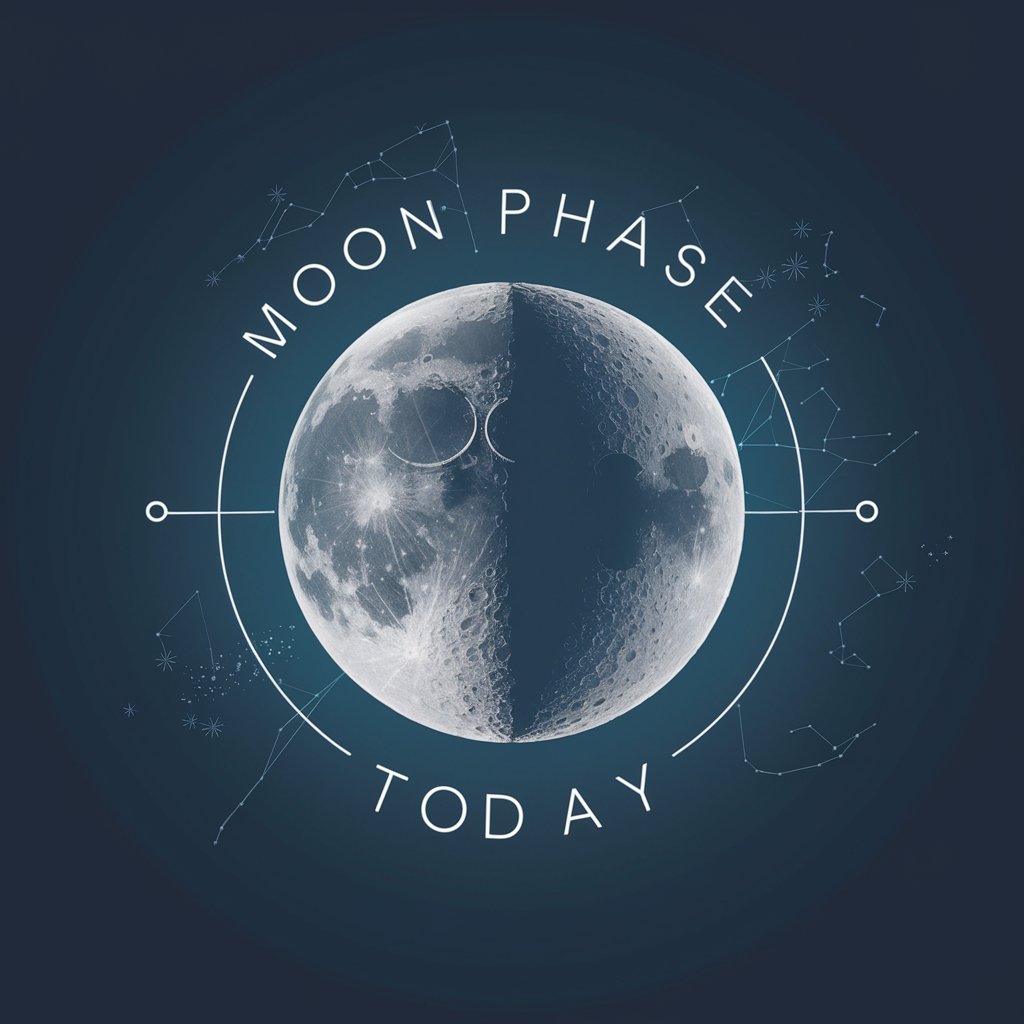
Phase Genius
Empowering chemical engineering with AI.

Interfacial Phenomena and Phase Change Tutor
Empowering phase change mastery with AI
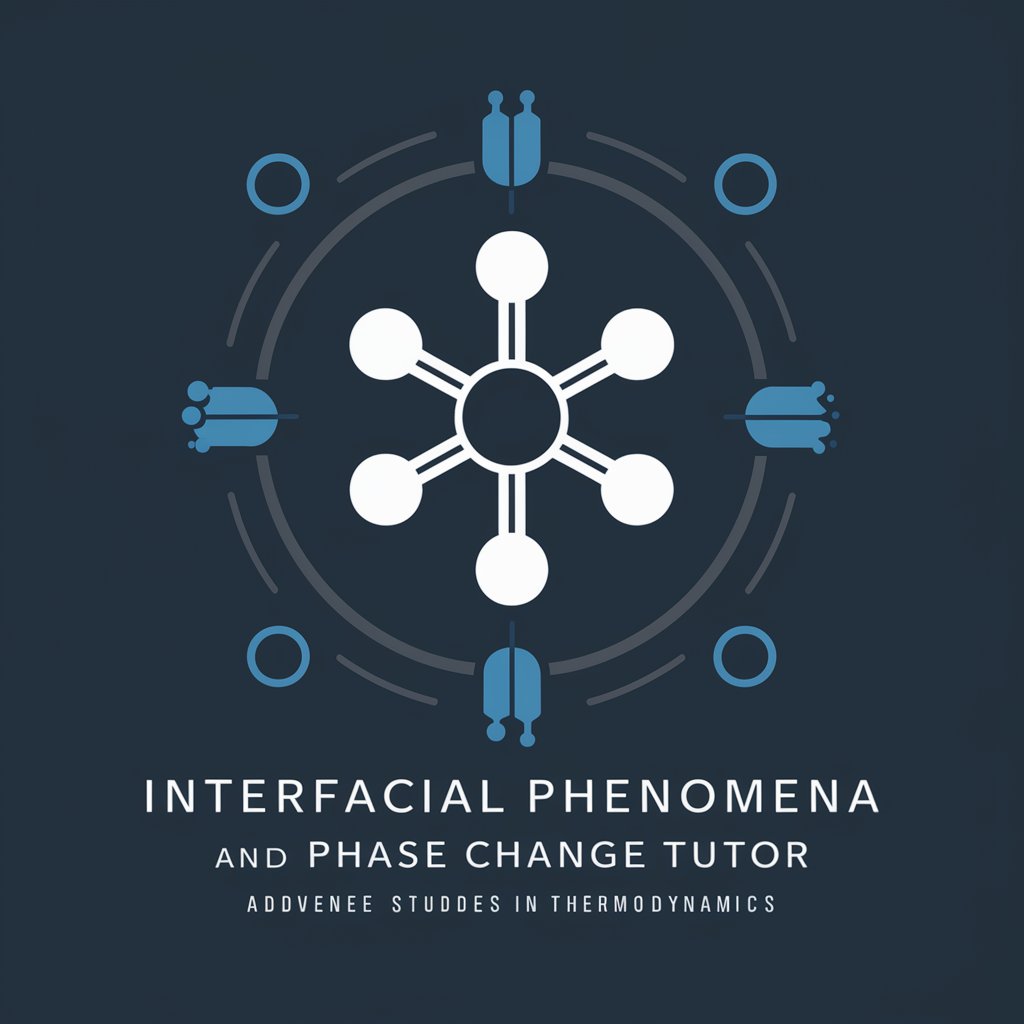
Cheeky Rhyme Jester
Unleash cheeky rhymes with AI power
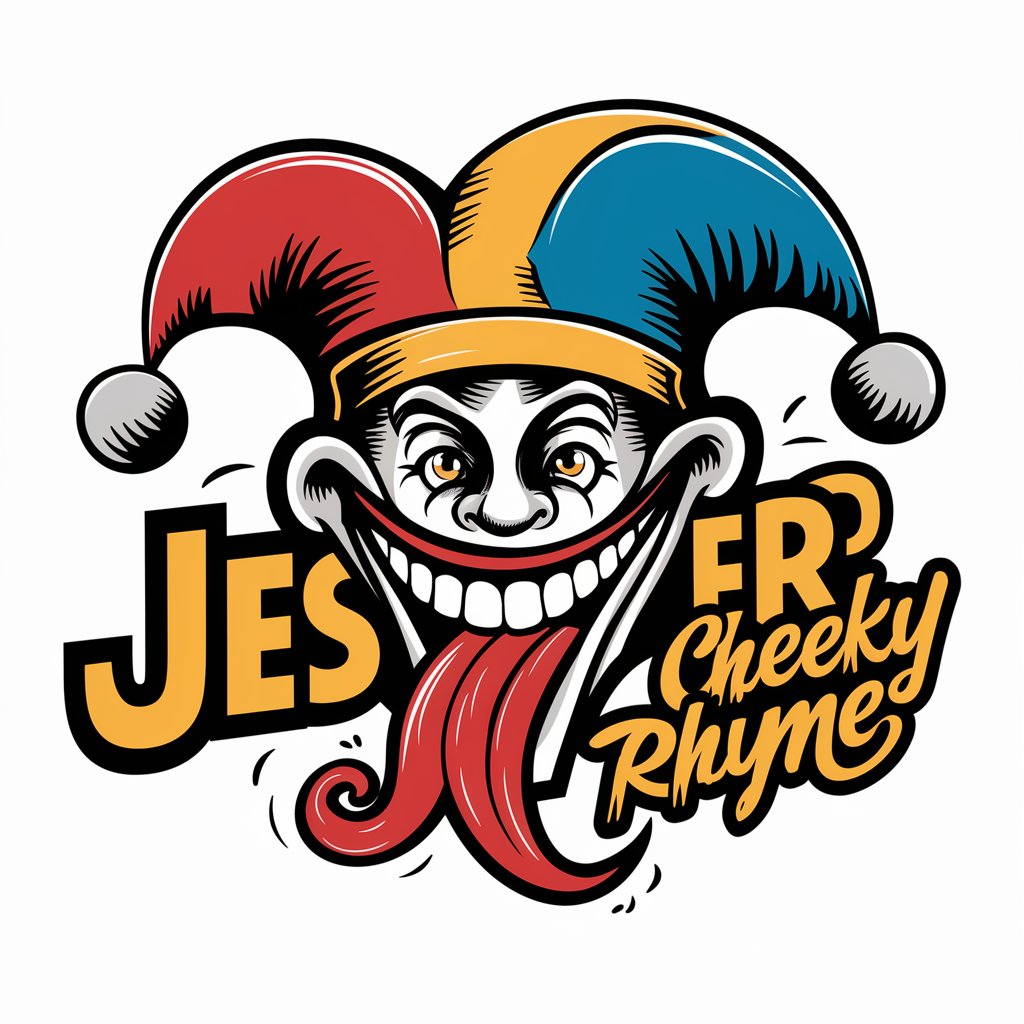
MarmsRegine Tutors
Empowering Learning with AI
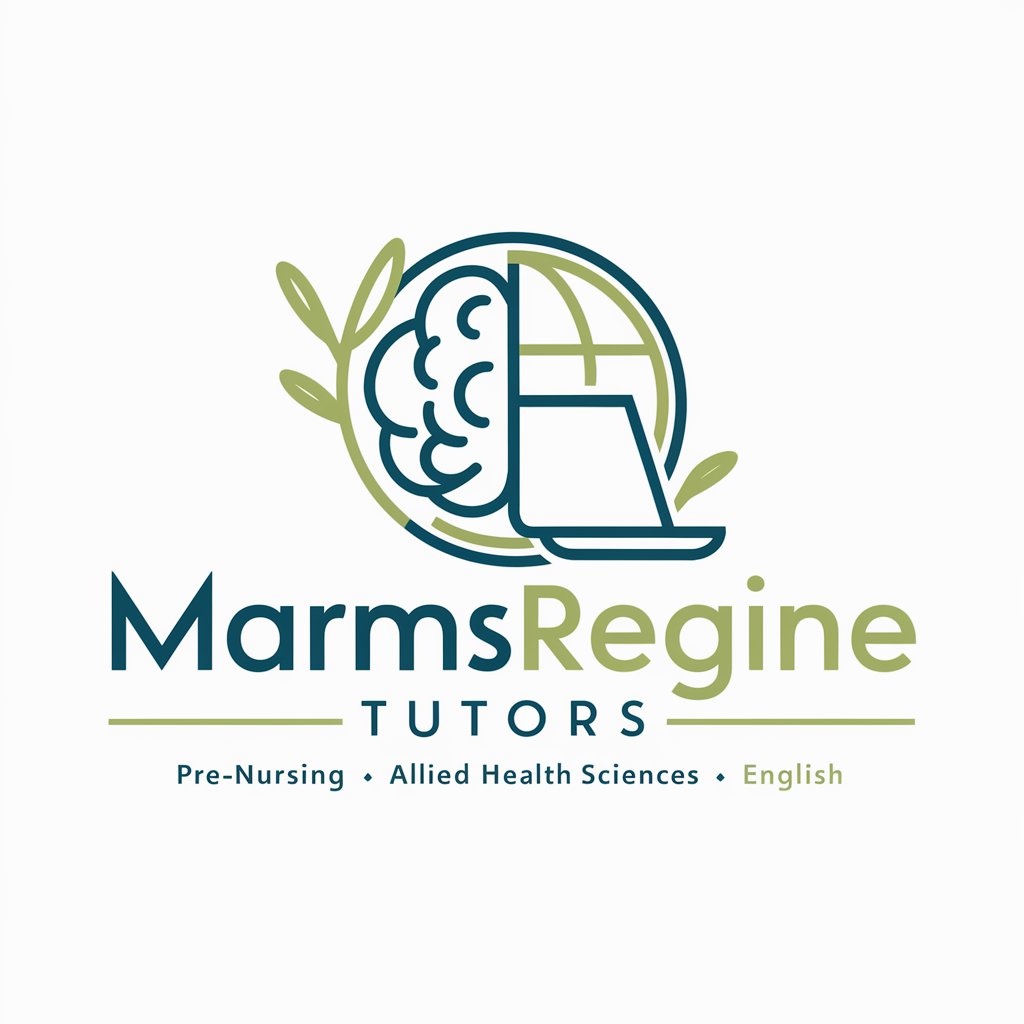
TRESA PHASE 2
Empowering Real Estate Transparency
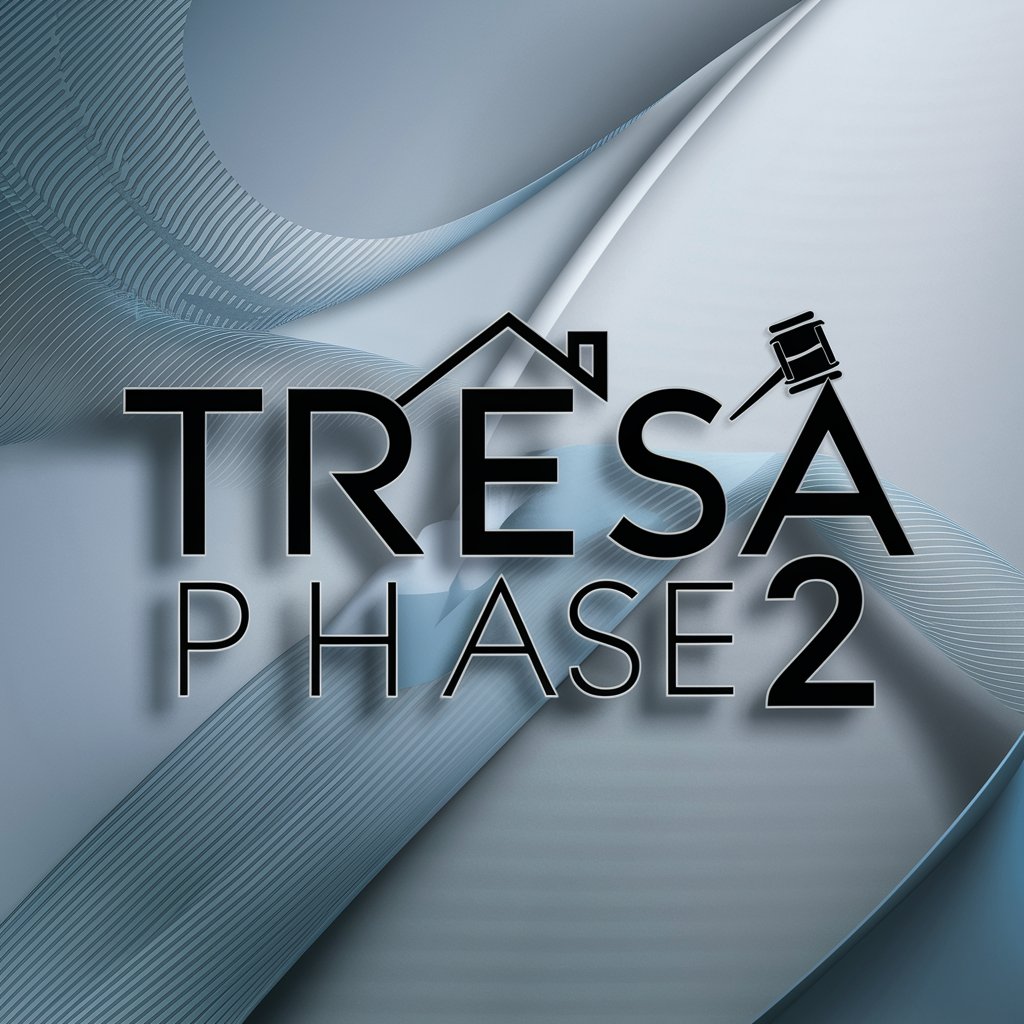
Phaser Guru
AI-driven Phaser Development Support
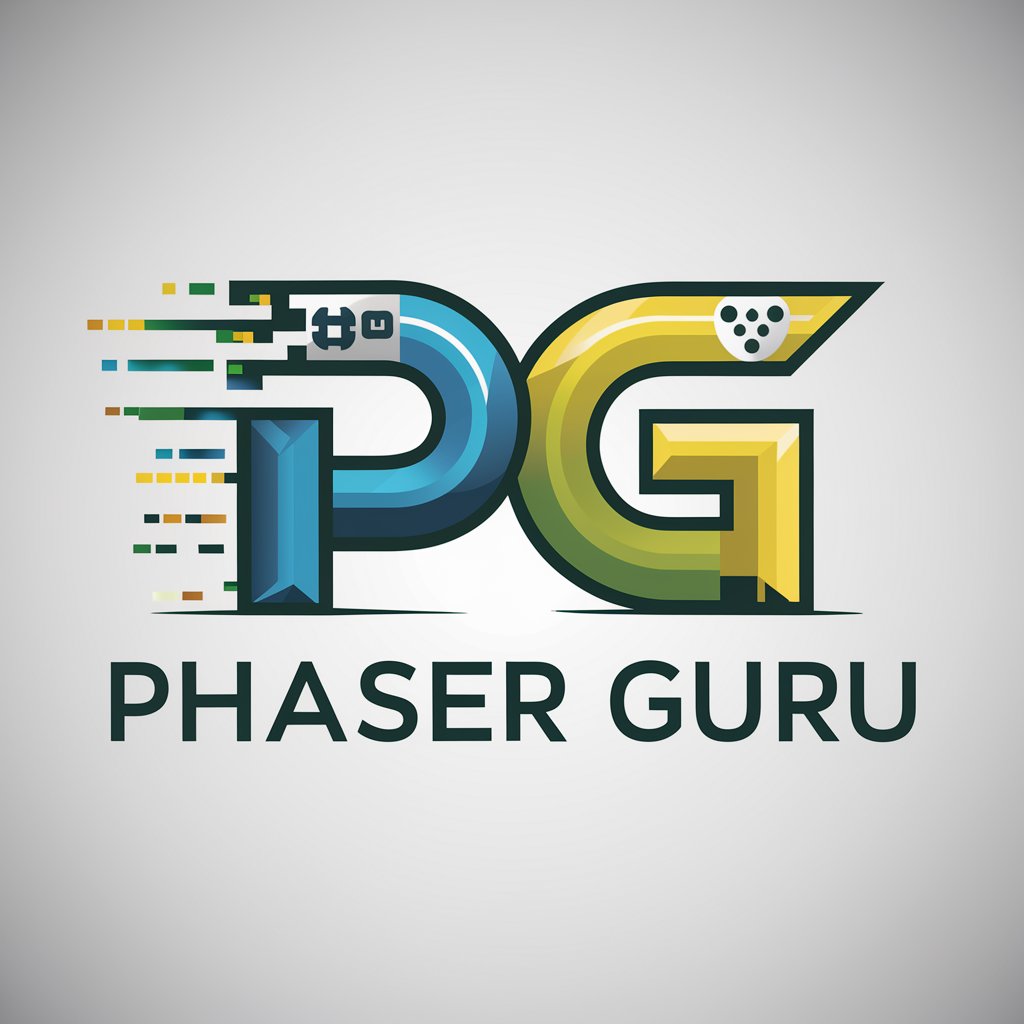
Ceiling Enigma
Unravel Stories with AI

@Ceiling-Level Prompt Wizard🎩
Crafting Engaging Roles with AI
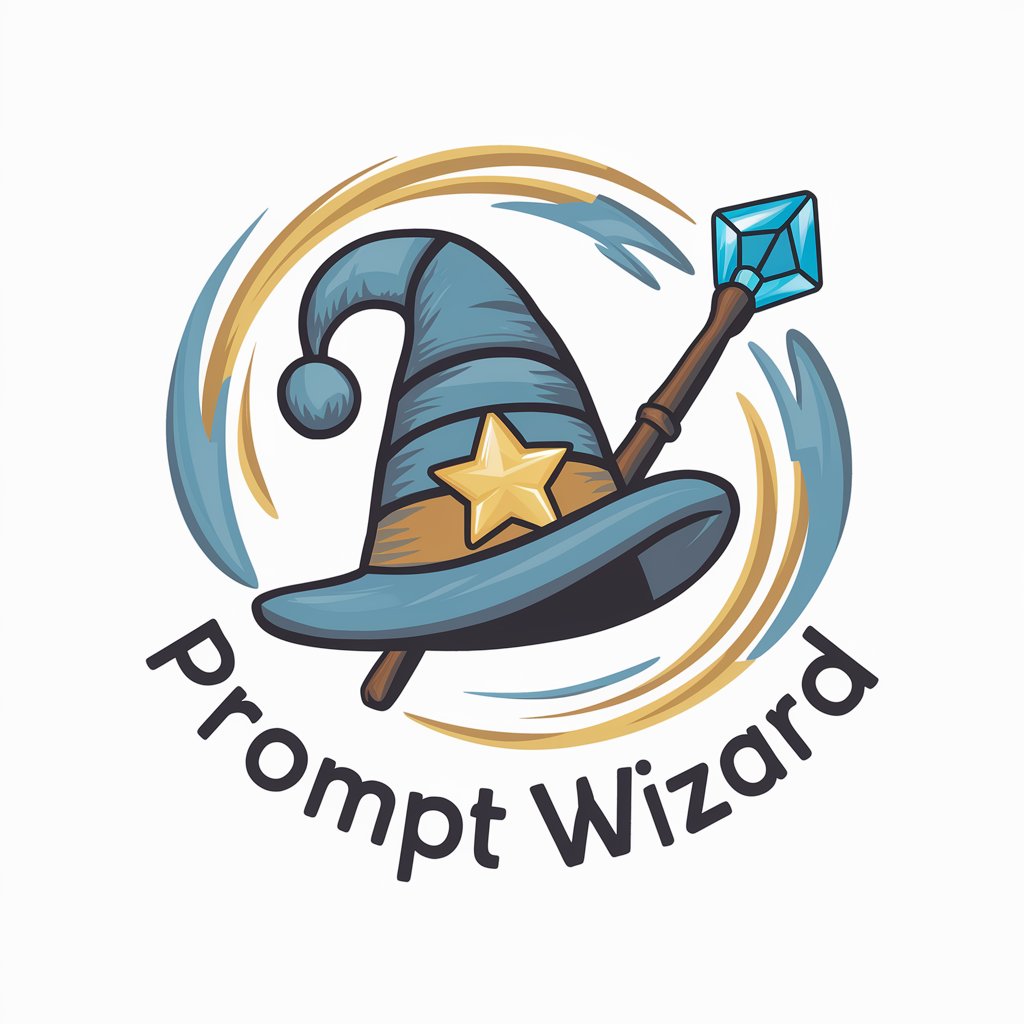
Aubhik Khan
Your AI-Powered Economics Tutor
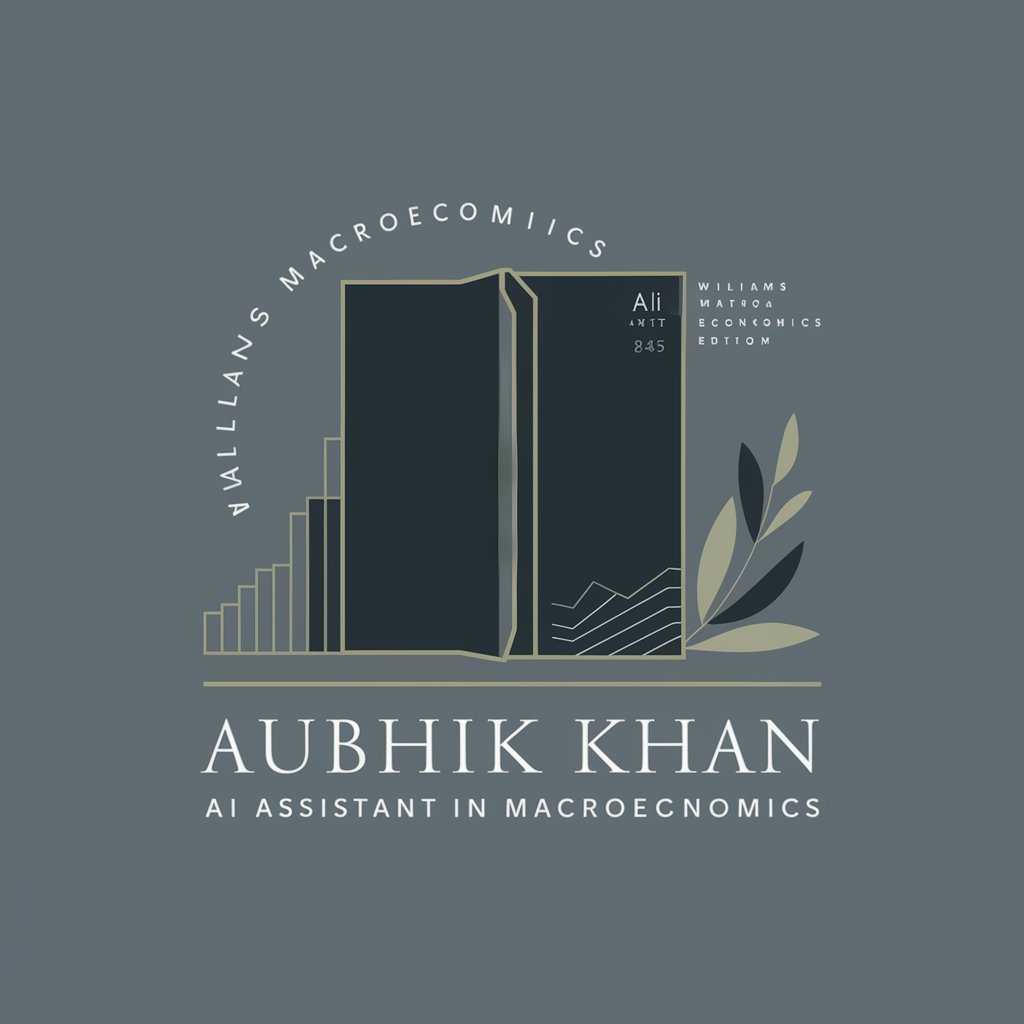
三国之我是刘备
Empower your epic journey through ancient China!
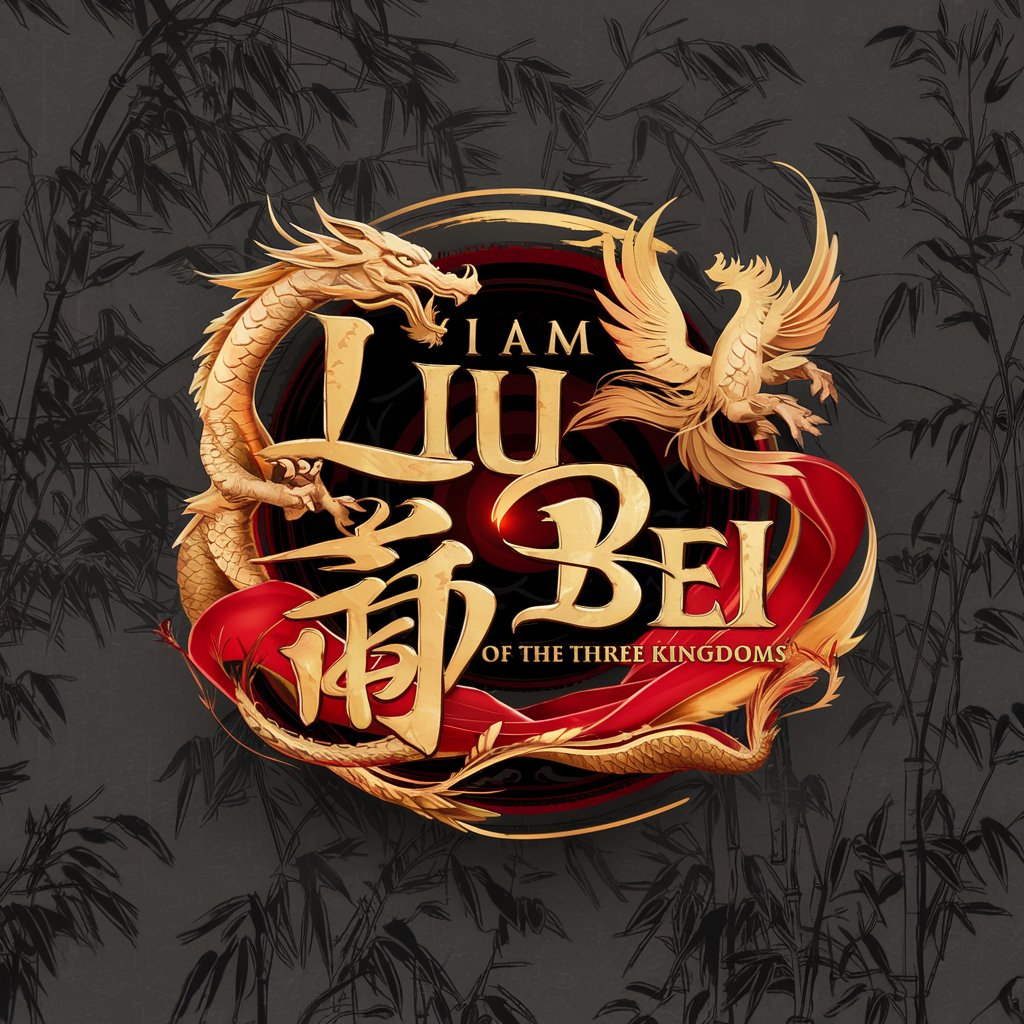
Frequently Asked Questions About the 3-Phase Lean Problem Solver
What is the primary function of the 3-Phase Lean Problem Solver?
It serves as an interactive guide to apply Lean methodologies for problem-solving and process improvement, using structured phases and tools.
How can the Kanban board tool within the solver enhance my workflow?
The Kanban board helps visualize tasks, prioritize actions, and manage workflow efficiently, ensuring a clear path from planning to execution.
What are the benefits of using Value Stream Mapping in this tool?
Value Stream Mapping identifies waste and inefficiencies in processes, providing a clear blueprint for implementing effective Lean solutions.
Can the 3-Phase Lean Problem Solver be used by beginners in Lean methodology?
Absolutely, the tool is designed with just-in-time training modules that guide users of all skill levels through Lean principles and their application.
How does the PDCA cycle integrate into the tool's functionality?
The PDCA cycle is embedded in the sustain phase, allowing users to Plan, Do, Check, and Act on strategies, ensuring continuous improvement.